3D Printing for Mechanical Parts: An Overview
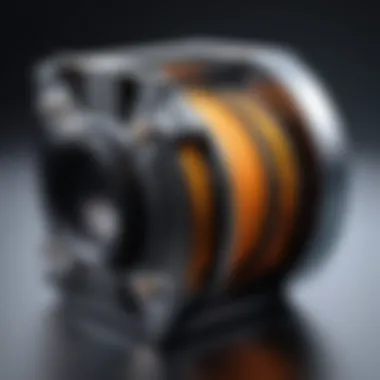
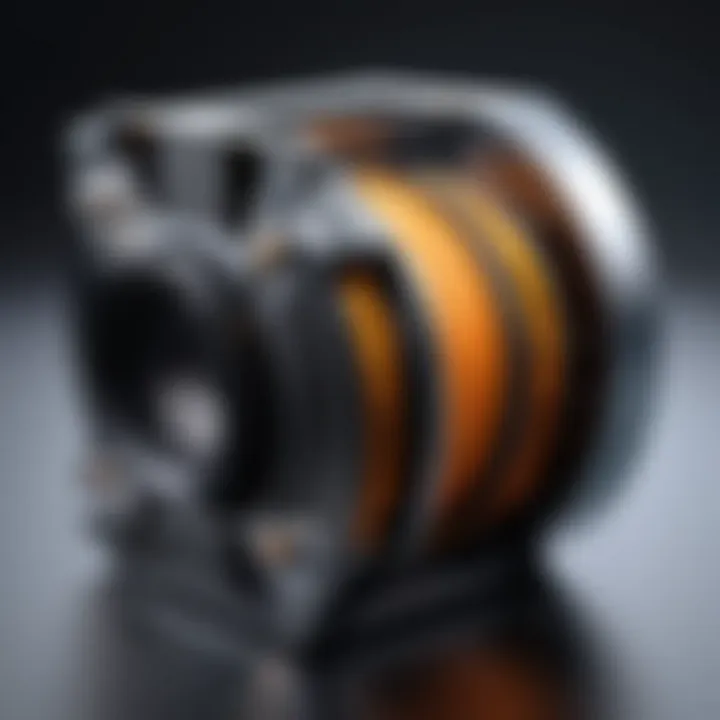
Intro
3D printing technology is rapidly transforming various industries, especially in the manufacturing of mechanical parts. This evolution has necessitated a deeper understanding of how 3D printing not only complements but sometimes replaces traditional production methods. The development of mechanical parts via this innovative approach presents unique challenges and opportunities that pertain to design, cost-efficiency, and overall effectiveness in production.
Understanding the relevance of this technological advancement requires looking closely at its features, benefits, and comparisons with alternative manufacturing processes. This overview aims to explore these areas in detail, creating a comprehensive guide that speaks to professionals across the spectrum—from IT specialists to decision-makers in both small and large businesses. By examining the nuances of 3D printing, readers will gain insights that are pertinent to their operational strategies and future planning.
Foreword to 3D Printing in Mechanical Manufacturing
3D printing significantly influences mechanical manufacturing. It enables the production of complex parts that were previously unfeasible with traditional methods. This technology not only improves efficiency but also allows for high levels of customization. Many industries, from aerospace to automotive, are adopting 3D printing due to its advantages over conventional manufacturing processes.
Defining 3D Printing
3D printing is also called additive manufacturing. It involves creating three-dimensional objects from a digital file. The process adds material layer by layer, building up the final product. The technology uses various methods, such as Fused Deposition Modeling (FDM) and Selective Laser Sintering (SLS). Each method has its own materials and applications.
This layer-wise construction contrasts with subtractive manufacturing, where material is removed from a solid block. The distinction is critical in understanding the flexibility and efficiency of 3D printing, especially in complex geometries that traditional methods cannot easily achieve.
Historical Context
The roots of 3D printing date back to the 1980s. The first method was stereolithography, developed by Charles Hull. It laid groundwork for future technologies. Over the years, numerous methods evolved, including FDM and SLS, leading to unique applications across industries.
In the 1990s, companies began to explore 3D printing for prototyping. However, the material and processing limitations restricted its use. Recent advancements have made 3D printing more accessible. The rise of desktop printers brought this technology to smaller businesses and hobbyists, expanding its influence.
Current Trends in 3D Printing
Today, 3D printing is gaining traction in various sectors. Industries emphasize rapid prototyping and customization. Notable trends include:
- Increased use of metal printing for critical components.
- Utilization of sustainable materials, such as biodegradable plastics.
- Growth in on-demand parts manufacturing, reducing inventory costs.
Various software tools streamline the design and production process. These tools enhance the user experience and allow engineers to work efficiently. The convergence of 3D printing with technologies like IoT and AI is also transforming how mechanical parts are manufactured. Businesses can now integrate data from their machines to optimize production.
Materials Used in 3D Printing for Mechanical Parts
The selection of materials in 3D printing plays a vital role in determining the functionality, durability, and overall success of mechanical parts. Understanding the types of available materials can guide engineers and designers in making informed choices that meet certain specifications and applications. This section will explore the common materials used in 3D printing, their properties, and criteria for selection.
Common Materials
Plastics
Plastics are among the most widely used materials in 3D printing for mechanical parts. Their versatility is a key factor contributing to their popularity. Thermoplastics, such as PLA (Polylactic Acid) and ABS (Acrylonitrile Butadiene Styrene), dominate the market due to their ease of use and cost-effectiveness.
Key Characteristic: The lightweight nature of plastics makes them especially useful in applications where weight reduction is essential.
Unique Feature: Plastics like ABS can withstand higher temperatures compared to other types, making them suitable for certain functional parts. However, their mechanical properties may not match those of metals, which limits their use in high-stress applications.
Metals
Metals offer superior strength and durability compared to plastics, making them an essential choice for many mechanical applications. Processes such as Selective Laser Melting (SLM) and Direct Metal Laser Sintering (DMLS) enable the precise layer-by-layer additive manufacturing of metallic components.
Key Characteristic: The high tensile strength of metals ensures that parts can endure significant loads and stresses without failure.
Unique Feature: Metals also provide enhanced thermal and electrical conductivity, which is critical in certain engineering applications. On the downside, the costs associated with metal 3D printing can be significantly higher than those of plastic printing, which can restrict its use in some projects.
Composites
Composites combine two or more materials to leverage the strengths of each. In 3D printing, composite materials, such as carbon fiber reinforced plastics, are gaining traction due to their enhanced mechanical properties. They are often used for lightweight structures that require additional strength.
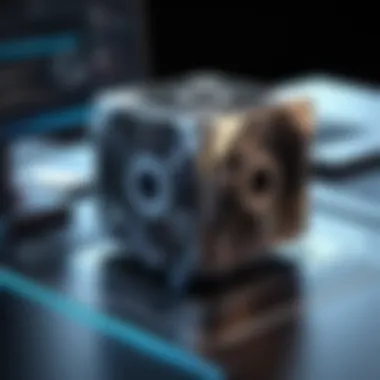
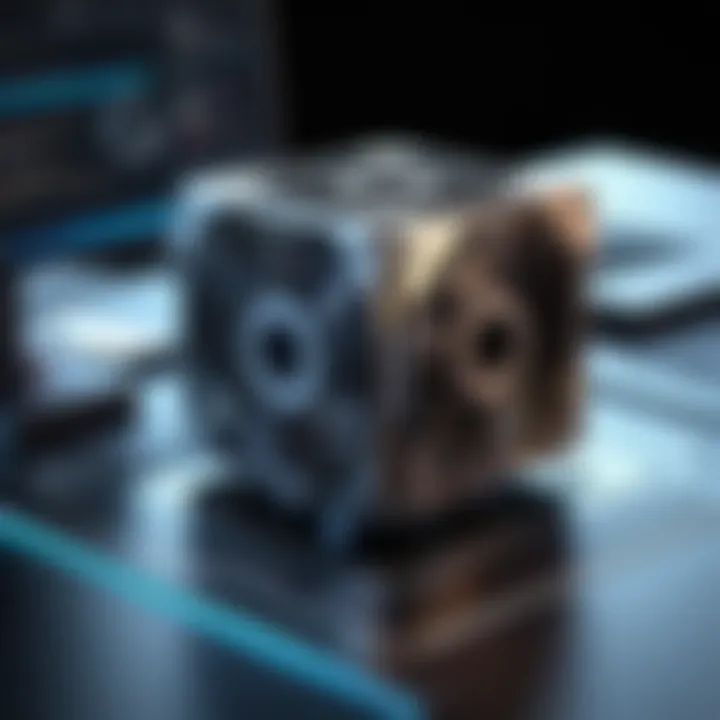
Key Characteristic: The high strength-to-weight ratio of composites makes them an attractive option for applications in aerospace and automotive industries.
Unique Feature: Composites often exhibit improved resistance to environmental factors, such as UV exposure and temperature fluctuations. However, processing these materials can be more complex and requires specialized equipment.
Material Properties
Material properties play a crucial role in the performance of the final 3D printed parts. Factors like strength, flexibility, and corrosion resistance define how well a material will perform in specific applications. Understanding these properties helps in ensuring that the printed components meet or exceed the expected performance criteria.
Material Selection Criteria
Choosing the right material for 3D printing mechanical parts involves several criteria:
- Mechanical Strength: Assessing the strength requirements for the intended application is essential.
- Thermal Stability: Determine if the material can withstand the operational temperature ranges.
- Cost: Evaluate the budget constraints while considering material prices.
- Ease of Printing: Some materials may be more difficult to print than others, influencing the choice.
- Post-Processing Needs: Consideration of any required post-processing can affect material selection.
These factors ensure that the chosen materials meet the specific performance expectations and design goals.
3D Printing Technologies for Mechanical Parts
The realm of 3D printing technologies plays a crucial role in the context of manufacturing mechanical parts. Each technology offers unique advantages and outcomes, which can affect various aspects of production including speed, cost, and quality. Understanding these technologies is key for professionals in mechanical engineering and design. They are the backbone of modern additive manufacturing and determine how effectively a mechanical part can be produced.
Fused Deposition Modeling (FDM)
Fused Deposition Modeling, or FDM, stands out as one of the most accessible and popular 3D printing technologies. It operates by extruding thermoplastic filament through a heated nozzle. As the nozzle moves, it lays down material layer by layer. This technology is particularly valued for its affordability and ease of use. FDM printers are widely available, making it feasible for both small businesses and large manufacturers to adopt.
However, FDM does come with certain limitations. The layer-by-layer approach can lead to visible layer lines, affecting the surface finish of the parts. In addition, the mechanical properties of FDM printed parts may not meet the requirements for high-stress applications. Yet, for prototyping and low-stress applications, FDM remains a practical choice.
Stereolithography (SLA)
Stereolithography is another essential technology in 3D printing. It utilizes a laser to cure liquid resin into hardened plastic. This process allows for incredible detail and precision, making SLA suitable for intricate designs and components. Parts printed using SLA generally have a smoother surface finish compared to FDM, which is critical in applications where aesthetic appearance is important.
Despite this, SLA printing can be time-consuming and requires post-processing to remove excess resin and cure the parts fully. The materials used in SLA are usually more expensive, which can limit its use for large-scale production. Nevertheless, for prototyping or in applications that demand high detail, SLA is often the preferred option.
Selective Laser Sintering (SLS)
Selective Laser Sintering employs a different method than FDM and SLA. It uses a laser to fuse powdered materials, such as nylon or metal, into solid parts. This technology allows for the production of strong and functional parts, making it ideal for mechanical applications. SLS does not require support structures, allowing for more complex geometries than some other methods.
The downside to SLS is the cost related to equipment and materials. Additionally, post-processing is often needed to remove any unused powder. However, due to its ability to produce durable parts in a range of materials, SLS is becoming increasingly popular within industries where functional prototypes are necessary.
Binder Jetting
Binder Jetting is a unique additive manufacturing technique that uses a liquid binding agent to join powdered materials. Unlike methods that fuse materials using heat, Binder Jetting allows for the production of parts with a wide variety of materials, including metals and ceramics. The process can generate complex geometries and full-color parts, appealing for applications in art and design.
The challenge with Binder Jetting lies in the post-processing requirements. Parts often require sintering or infusing to achieve strength and durability. While effective for prototypes and decorative elements, the performance characteristics may not always match those required for critical mechanical applications.
Understanding these 3D printing technologies is vital for selecting the right method for specific mechanical parts. The choice hinges on the project requirements, budget constraints, and desired part characteristics. Therefore, careful evaluation of these technologies leads to more informed decisions in mechanical engineering.
Design Considerations for 3D Printed Mechanical Parts
Design considerations for 3D printed mechanical parts play a crucial role in determining the success of a project. The shift to additive manufacturing introduces unique challenges and opportunities compared to traditional manufacturing methods. Understanding how to leverage these considerations effectively can lead to significant enhancements in performance, efficiency, and cost-effectiveness. Key elements include the use of software tools, optimization practices, and the inherent challenges in the design phase of 3D printing.
Computer-Aided Design (CAD) Software
Computer-Aided Design (CAD) software is fundamental for creating detailed 3D models needed in 3D printing. It allows engineers to visualize and refine designs before production, ensuring that all specifications are met. Popular CAD software such as SolidWorks, Autodesk Inventor, and Fusion 360 serve as platforms for modeling complex geometries that are often less feasible in traditional manufacturing.
Using CAD facilitates quick iterations. Designers can simulate how a part will behave under different conditions. This testing phase is essential for minimizing errors and ensuring the final product meets performance standards. Additionally, CAD models can be directly exported into slicing software, which prepares the models for printing, thus streamlining the workflow.
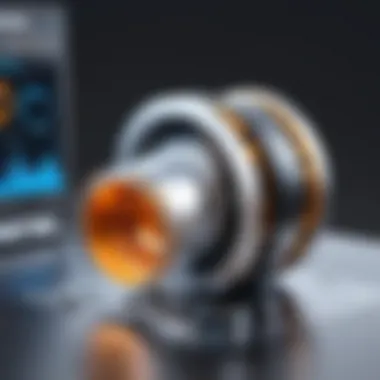
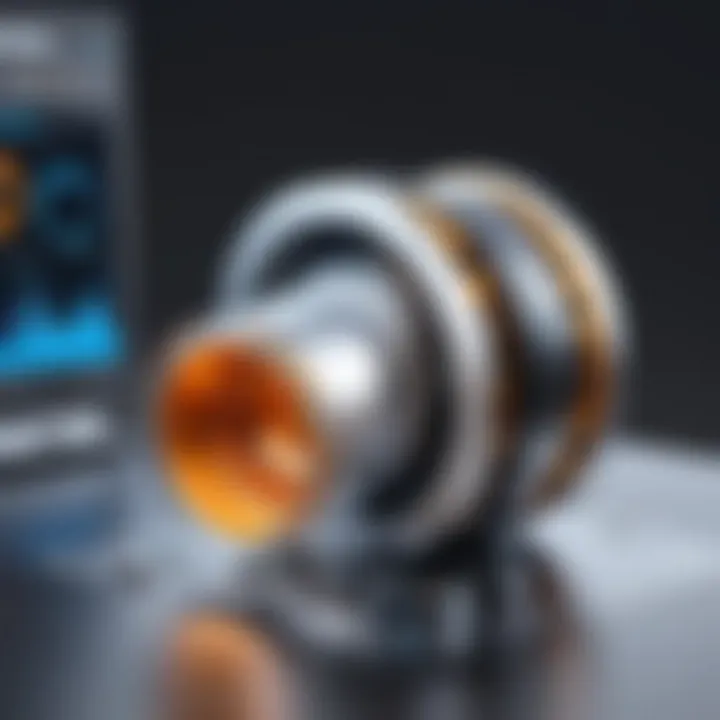
Design Optimization Practices
Design optimization is crucial for maximizing the advantages of 3D printing technology. First and foremost, lightweighting is often a priority. This involves removing unnecessary material without compromising the part's strength. Techniques such as topology optimization help in creating support structures that retain strength while minimizing material usage. Furthermore, incorporating features such as lattice structures can significantly enhance part performance.
Another important optimization practice is ensuring proper orientation during printing. The orientation affects mechanical properties significantly. For instance, printing a part on its side can yield better strength along the layer lines compared to a vertical orientation. Aspects like thermal distortion and cooling rates should also be considered during the design phase to prevent warping or other issues in the final product.
Challenges of Additive Manufacturing Design
Despite the advancements, there are challenges inherent in additive manufacturing design. Dimensional accuracy is a concern; parts may not always come out as accurately as modeled. Each printer has specific tolerances and it is vital to understand these limits when designing parts. Moreover, layer adhesion issues can arise, causing structural weaknesses in overhangs or intricate designs.
Post-processing is also a critical consideration. Many parts require cleaning, curing, or supports removal after printing. These steps can add time and cost to the production process. Designers must account for these factors during their planning stages and design parts that mitigate the need for extensive post-processing where possible.
Applications of 3D Printing in Mechanical Engineering
The integration of 3D printing within mechanical engineering is not just an evolution; it represents a pivotal shift in how components are designed, produced, and employed across various sectors. It offers distinct advantages and the potential to address traditional manufacturing constraints. The significance of this technology lies in its ability to enhance efficiency, improve customization, and facilitate rapid prototyping. Moreover, it enables innovation in product design that aligns with modern engineering needs. Below, we explore three key aspects of 3D printing applications in this field.
Prototyping and Testing
One of the primary applications of 3D printing is prototyping. In conventional manufacturing, creating a prototype can be time-consuming and costly. With 3D printing, however, engineers can produce prototypes quickly and at a fraction of the cost. This technology allows for rapid iterations, enabling designers to test multiple variations of a part in a shorter timeframe.
- Benefits of Rapid Prototyping
- Cost-effective method for producing prototypes.
- Reduction in time from concept to functional model.
- Possibility to test complex geometries that traditional methods cannot easily achieve.
The ability to prototype quickly fosters a culture of innovation. Engineers can take risks with designs they might not otherwise pursue, knowing they can validate ideas swiftly.
Production of End-Use Parts
In addition to prototyping, 3D printing has gained traction in the production of end-use parts. Industries such as aerospace, automotive, and healthcare leverage this technology to manufacture components that meet specific requirements.
- Applications in Various Industries
- Aerospace components that are lightweight yet strong.
- Custom implants in healthcare tailored to individual patients.
- Automotive parts that require complex designs and rapid production cycles.
3D printing allows for on-demand production, reducing storage costs and excess inventory. It also streamlines the supply chain by producing parts closer to the point of need.
Customization and Personalization
The ability to easily customize parts is another major advantage of 3D printing. This technology supports bespoke manufacturing, allowing for modifications tailored to individual specifications without incurring significant costs. Personalized products improve user satisfaction and can lead to a competitive advantage.
- Customization Opportunities
- Development of specialized features in mechanical parts.
- Ability to create items that cater directly to user preferences and needs.
- Reduction in lead times with direct manufacturing capabilities.
Economic Implications of 3D Printing for Mechanical Parts
The economic implications of 3D printing technology in the production of mechanical parts are significant and multifaceted. As industries continue to adopt this technology, its impact on cost structures and operational efficiencies becomes increasingly evident. Understanding these implications is essential for businesses weighing the investment in additive manufacturing processes. This section delves into the financial considerations and transformative power of 3D printing in today's market.
Cost-Benefit Analysis
Conducting a cost-benefit analysis for 3D printing involves examining both initial investments and ongoing costs. The startup costs can include the purchase of 3D printers and materials, software licensing, and training employees. However, these costs vary widely depending on the specific technology chosen. For instance, Fused Deposition Modeling (FDM) printers are generally more affordable compared to Selective Laser Sintering (SLS) machines.
Once established, the potential benefits of 3D printing can outweigh these starting expenses. These benefits include:
- Reduced Material Waste: Unlike traditional subtractive methods, 3D printing produces parts layer by layer, allowing for more efficient use of materials.
- Shorter Lead Times: The ability to produce components on-demand can substantially decrease the time from design to production.
- Lower Shipping Costs: Localized production reduces reliance on extended supply chains, cutting shipping expenses.
- Customization: The technology allows for easier customization of parts, which can cater to specific customer needs without significant additional cost.
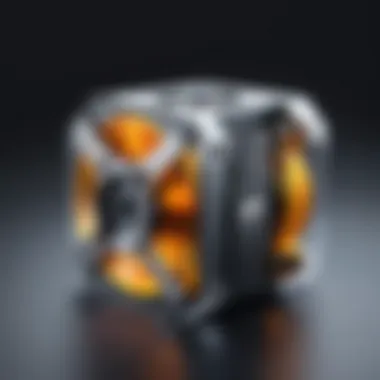
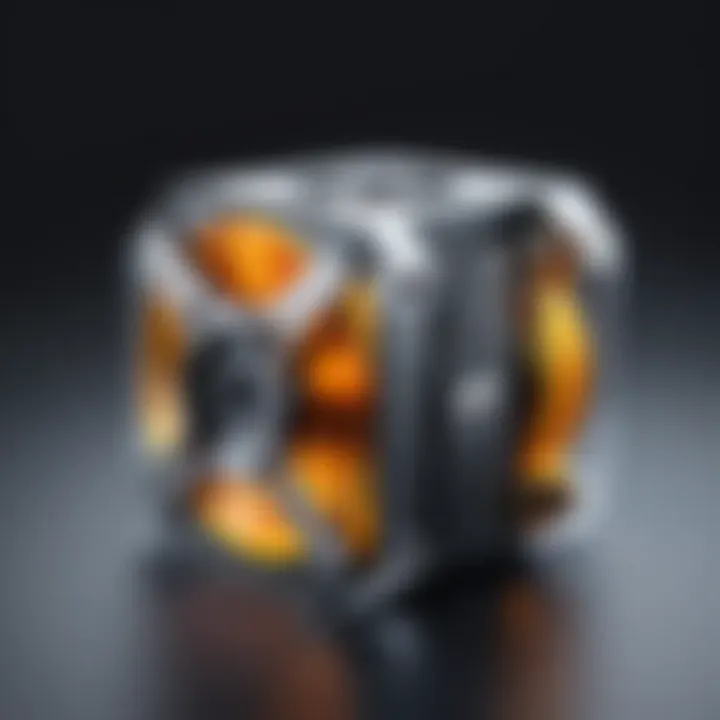
"In many cases, the overall savings from reduced waste and improved speed can offset the initial costs of investment."
Impact on Supply Chains
3D printing is reshaping traditional supply chains by introducing a more decentralized production model. One of the critical economic implications is the potential to simplify supply chains significantly. Here are some ways in which this is happening:
- Local Production: Companies can shift from centralized factories to local production, decreasing transportation fees and time.
- On-Demand Manufacturing: Parts can be produced as required rather than building up inventory, which reduces storage costs and minimizes the risk of obsolescence.
- Simplified Logistics: Fewer intermediaries in the supply chain can streamline logistics, improving overall efficiency.
- Resilience: Localized production can enhance resilience against global supply chain disruptions, such as those experienced during the COVID-19 pandemic.
Technical Challenges of 3D Printing Mechanical Parts
3D printing offers numerous advantages, yet it comes with its own set of technical challenges that can affect quality and production efficiency. Understanding these challenges is crucial for effective implementation of 3D printing in mechanical part manufacturing. This section will address three significant challenges: dimensional accuracy, layer adhesion issues, and post-processing requirements. Each of these subtleties plays a vital role in achieving reliable products, and they warrant careful consideration during the design and production phases.
Dimensional Accuracy
Dimensional accuracy refers to how closely a 3D printed part matches the intended design specifications. This is particularly important in mechanical applications, where even slight deviations can lead to misalignment or mechanical failure. Factors influencing dimensional accuracy include printer calibration, material shrinkage, and environmental conditions.
For instance, the type of filament or resin used can expand or contract more than expected as it cools, altering dimensions. A proper calibration routine and regular maintenance is necessary to maintain accuracy. Employing specialized software can help in predicting these changes and compensating for them during the design phase.
In summary, manufacturers must pay keen attention to the dimensional accuracy of their parts to ensure functionality and reliability in their applications.
Layer Adhesion Issues
Layer adhesion is critical for the mechanical integrity of printed parts. Poor adhesion between layers can lead to delamination, which reduces strength and could result in part failure under stress. The reasons for weak layer adhesion include insufficient printing temperature, incorrect speed, and improper layer height settings.
Effective strategies for improving layer adhesion include:
- Optimizing temperature settings: Ensuring that the printing temperature is within the optimal range for the material used can enhance bonding.
- Adjusting print speed: Sometimes slowing down the print speed allows more time for each layer to bond properly before the next is applied.
- Choosing suitable materials: Some materials have better layer adhesion properties than others. Selecting the right material can significantly mitigate this issue.
Post-Processing Requirements
Post-processing is often required to enhance the finish and performance of 3D printed mechanical parts. This stage can involve techniques such as sanding, sealing, or painting, which can significantly improve the aesthetic and functional qualities of a part. In addition, some applications may require additional treatments to enhance thermal or chemical resistance.
Common post-processing techniques include:
- Sanding: To achieve a smooth surface finish, sanding is a standard practice. This step helps remove the visible layer lines left from the printing process.
- Annealing: This is heating the printed part to increase its crystallinity, thus improving mechanical properties.
- Surface treatments: Such as applying resins or coatings to protect against wear and environmental factors.
While post-processing enhances the final product, it adds time and costs to production. Organizations must weigh the benefits against these added factors during the planning phase.
Future Trends in 3D Printing for Mechanical Parts
The future of 3D printing in mechanical parts manufacturing is pivotal. Understanding future trends allows businesses to adapt and remain competitive. With rapid technological advancement, the integration of novel materials and new technologies enhances the capabilities of 3D printing. These innovations not only optimize manufacturing processes but also enable the production of more complex and efficient designs. Technologies evolving in this space promise better-quality outputs and reduced production time.
Advancements in Materials Science
Materials science is advancing considerably in the realm of 3D printing. Innovations in this field introduce new options beyond the traditional plastics and metals. For example, bio-materials and high-performance alloys are gaining traction. These materials boast superior strength and lighter weight, which are essential in industries such as aerospace and automotive. New synthesis techniques are also allowing for tailored material properties.
Adopting these new materials can lead to enhanced performance of mechanical parts. They could also reduce costs through more efficient use of resources. Thus, staying informed about materials science trends is crucial for success in adopting 3D printing technologies.
Integration with Other Technologies
IoT
The Internet of Things (IoT) shapes the future of 3D printing significantly. IoT connects devices and allows them to communicate. This connectivity can monitor the performance of printers in real-time. It helps in collecting data that can inform maintenance schedules and operational adjustments. This is vital because optimizing equipment directly correlates with production efficiency.
A key characteristic of IoT is its capability for remote monitoring, which enables businesses to gain insights into their manufacturing processes. Moreover, it helps in predictive maintenance, reducing unexpected downtimes. However, the integration of IoT comes with concerns regarding data security, which must be addressed to leverage its full potential.
AI in 3D Printing
Artificial Intelligence (AI) brings transformative potential to 3D printing. Algorithms can optimize printing parameters, resulting in better quality and speed of production. AI can analyze vast datasets from previous prints to identify patterns. It helps in making predictions about future performance outcomes, which is beneficial for design validation.
A pivotal characteristic of AI is its learning capability. As it processes more data, it becomes increasingly efficient at improving production protocols. This not only enhances productivity but also prepares systems for complex designs. However, AI implementation requires significant upfront investment and expertise. Despite these challenges, the long-term benefits make it a compelling choice for organizations looking to push the boundaries of 3D printing.
The shift towards advanced materials and integration with IoT and AI heralds a transformative era for 3D printing, ensuring enhanced functionality and efficiency across mechanical parts manufacturing.