Top Warehouse Management System Software Solutions
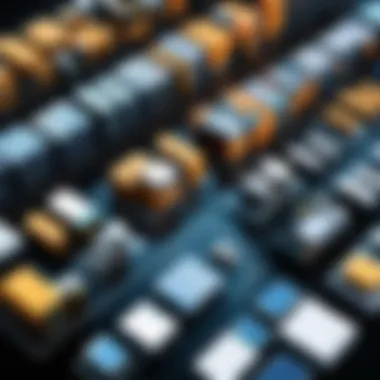

Intro
Warehouse Management Systems (WMS) are vital for managing logistics and enhancing operational efficiency. In the fast-paced world of supply chain management, companies require software solutions that not only meet their current needs but also adapt to future demands. A well-chosen WMS can improve inventory accuracy, streamline processes, and ultimately lead to higher customer satisfaction.
Key Features and Benefits
Overview of Features
WMS software offers a variety of features designed to optimize warehouse operations. Key features include:
- Inventory Management: Tracks stock levels, locations, and movements in real-time.
- Order Fulfillment: Automates order processing, ensuring quick and accurate shipments.
- Labor Management: Helps in tracking employee performance and productivity.
- Reporting and Analytics: Provides insights into operations through detailed reporting features.
- Integration Capabilities: Allows syncing with other systems like ERP and CRM software.
These features are essential for supporting various logistical needs and enhancing overall productivity.
Benefits to Users
The benefits of implementing a robust WMS are numerous. Users can expect:
- Increased Efficiency: Streamlined operations lead to significant time savings.
- Reduced Errors: Automation reduces the likelihood of human error in inventory management.
- Cost Savings: Improved inventory turnover and reduced carrying costs contribute to lower operational costs.
- Scalability: A good WMS can grow with the business, accommodating increased volumes and complexity.
Adopting a WMS is not merely beneficial; it is often necessary for businesses aiming to remain competitive in today’s market.
Comparison with Alternatives
Head-to-Head Feature Analysis
When evaluating WMS solutions, comparing them against alternatives is crucial. For example, systems like Oracle NetSuite and SAP Extended Warehouse Management (EWM) have distinct advantages. A detailed analysis reveals:
- Oracle NetSuite: Offers integrated financial functionality along with inventory management, making it a strong contender for larger enterprises that need seamless operations.
- SAP EWM: Known for its extensive options for complex warehouse structures, it excels in industries handling various inventory types.
Both have different strengths that cater to varying business requirements.
Pricing Comparison
Pricing can vary widely among WMS solutions. Factors influencing the cost include deployment method (cloud vs. on-premise), scale, and service agreements. Generally:
- Cloud Solutions: Tend to have lower upfront costs, with subscription fees reducing initial investment.
- On-Premise Solutions: Often require significant investment in hardware and software but may offer lower long-term costs depending on the business scale.
It's essential to evaluate total cost of ownership when selecting a solution, considering both implemented features and ongoing maintenance.
"Investing in a WMS is an investment in the future efficiency of your logistics operations."
Prelims to WMS Software
Understanding Warehouse Management System (WMS) software is crucial for businesses that manage extensive logistics operations. The role of WMS software has evolved into a foundational asset for optimizing efficiency, accuracy, and cost-effectiveness in supply chain management. Organizations from large enterprises to small businesses can benefit from implementing the right WMS solution. This section highlights the significance of WMS software while addressing its core functionalities and impacts on operational performance.
Definition and Purpose
A Warehouse Management System is software designed to support and optimize warehouse functionality and distribution center management. Its primary purposes include tracking inventory levels, managing stock locations, and facilitating order processing. By automating manual tasks and reducing errors, WMS software increases warehouse productivity. It allows managers to gain greater visibility into operations, which ultimately leads to improved service levels. In today's fast-paced business environment, a robust WMS is no longer optional but a necessity for maintaining competitiveness.
Historical Context
The concept of warehouse management has changed significantly over the years. Initially, it relied heavily on manual processes and paper-based systems. The introduction of barcode scanning in the late 20th century marked a pivotal advancement in enhancing efficiency. However, as e-commerce expanded in the following decades, the demand for more sophisticated WMS solutions grew substantially. Modern WMS software now integrates seamlessly with other supply chain technologies, reflecting the increased complexity of global logistics.
"The evolution of warehouse management systems has mirrored the rapid growth of technology in logistics. Understanding its history helps us appreciate the current dynamics of supply chain management."
Businesses must appreciate these developments to make informed decisions regarding WMS solutions today.
Key Features of WMS Software
In the realm of logistics and supply chain, Warehouse Management System (WMS) software plays a pivotal role in streamlining operations. Understanding the key features of WMS software is essential for organizations aiming to enhance their warehouse efficiency and reduce operational costs. These features not only cater to specific logistical needs but also ensure smoother workflows.
Inventory Management
Inventory management is perhaps the most critical feature of any WMS. It allows businesses to maintain optimal stock levels, reducing both overstock and stockouts. Using this feature, companies can achieve better visibility into their inventory holdings. This visibility helps in tracking items in real-time, forecasting demand, and planning purchases accordingly.
Moreover, efficient inventory management leads to better customer satisfaction. When products are available as needed, businesses can fulfill orders quickly and accurately. This contributes to improved sales and customer loyalty.
Order Fulfillment
Order fulfillment functionalities are another significant component of WMS software. They encompass the processes involved in picking, packing, and shipping products. A reliable WMS software automates these tasks, minimizing human error and speeding up order processing. As a result, organizations see an improvement in their service levels.
An efficient order fulfillment system ensures that orders are processed accurately and dispatched promptly. Customers expect quick delivery, and the speed of fulfillment often determines customer satisfaction. Therefore, a WMS that excels in this area is invaluable for any business.
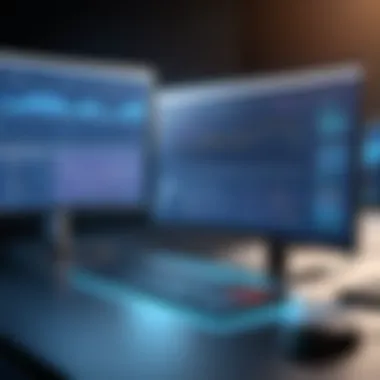

Reporting and Analytics
The ability to generate detailed reports and perform analytics is a fundamental feature in WMS software. This functionality allows managers to gain insights into operations and make informed decisions. With real-time data at their fingertips, businesses can track performance metrics, such as order processing times and inventory turnover rates.
Data-driven decision-making empowers businesses to identify bottlenecks and inefficiencies in their operations. Consequently, managers can devise strategies to enhance productivity and make necessary adjustments in real-time, leading to sustained operational improvements.
Integration Capabilities
Integration capabilities are essential for WMS software to function effectively within the broader technological landscape of a business. A good WMS will seamlessly integrate with other systems, including Enterprise Resource Planning (ERP) software, Customer Relationship Management (CRM) systems, and e-commerce platforms. This interconnectedness facilitates the flow of information across various departments.
Furthermore, integration enables streamlined operations by ensuring that all systems work in harmony. For instance, updated inventory levels in the WMS can be reflected in the ERP system, improving accuracy in financial forecasting and resource allocation. Thus, choosing a WMS that offers robust integration is crucial for maximizing operational efficiency.
Benefits of Implementing WMS Software
Implementing a Warehouse Management System (WMS) offers various benefits to businesses engaged in logistics and supply chain operations. These systems are designed to simplify processes, improving overall productivity and operational output. With clear benefits in areas such as efficiency, accuracy, and cost management, a WMS can become an essential asset in modern warehousing and inventory management.
Enhanced Efficiency
One of the most significant advantages of adopting a WMS is the enhancement of operational efficiency. A well-implemented WMS streamlines warehouse operations by automating various tasks. For instance, by identifying optimal picking paths, employees can reduce the time spent retrieving products. Furthermore, automated tracking and inventory counts ensure that stock levels are accurate, which minimizes delays and errors in order processing.
- Task Automation: Many routine tasks can be automated, allowing staff to focus on more strategic activities.
- Real-time Tracking: Businesses can monitor inventory levels and order statuses in real time, fostering informed decision-making.
- Improved Layout Optimization: A WMS can offer insights on the most efficient layout for a warehouse, minimizing travel time for picking products.
In summary, enhanced efficiency leads to faster order fulfillment and better resource utilization, ultimately resulting in higher customer satisfaction.
Increased Accuracy
Accuracy is another crucial factor that WMS software significantly improves. Manual stock management often leads to discrepancies and errors that can be costly for businesses. A WMS employs various technologies, such as barcode scanning and RFID tracking, to ensure that the right products are picked and shipped.
- Error Reduction: The system minimizes human error during all processes, from inventory counts to order fulfillment.
- Inventory Accuracy: Real-time updates ensure that the information regarding available stock is current, reducing instances of overstock or stockouts.
- Order Verification: Automatic order verification processes help confirm that the correct items are picked for shipping.
The culmination of these improvements leads to a more reliable service, fostering trust and loyalty among clients and customers.
Cost Reduction
Implementing a WMS can lead to significant cost reductions. This is partly due to increased efficiency and accuracy, but there are additional aspects to consider. By optimizing warehouse operations, a WMS helps reduce labor costs and overhead associated with inventory management.
- Lower Labor Costs: Streamlined processes mean less time is needed for staff to complete tasks, which can translate into fewer employees required.
- Reduced Waste: Improved inventory accuracy leads to fewer expired or obsolete products, minimizing loss.
- Improved Supplier Relationships: Accurate forecasting and inventory management lead to better ordering practices, thus reducing costs associated with excess stock.
Factors to Consider When Choosing WMS Software
Choosing the right Warehouse Management System (WMS) is crucial for optimizing inventory and improving overall efficiency. Various factors shape the decision-making process. Each element plays a significant role in ensuring that the selected software meets the specific needs of the organization and enhances operational effectiveness.
Business Size and Scale
When selecting WMS software, it is essential to consider the size and scale of your business. Smaller warehouses may benefit from simpler systems, while larger operations require robust solutions. A small enterprise likely needs a straightforward interface and fewer features. Conversely, large businesses necessitate more complex functionality capable of handling various processes like multi-location management and extensive reporting.
Choosing software that aligns with business size ensures that the system can handle growth effectively. Many WMS solutions offer tiered pricing models based on the number of users or features, which may also help keep initial costs down while providing the required scalability.
Industry-Specific Needs
Different industries have distinct logistical requirements. For instance, the regulations and inventory demands in the pharmaceutical sector vastly differ from those in retail. Therefore, understanding industry-specific needs is vital in selecting the right WMS. It’s not just about the features available; it’s about ensuring those features can meet compliance and operational standards relevant to your sector.
For example, a food distribution company may require temperature control capabilities, whereas a fashion retailer might prioritize a user-friendly interface for fast order fulfillment. Identifying these unique needs helps zero in on WMS solutions that are not only compliant but also enhance operational efficiencies.
Budget Constraints
Finally, budget is a significant determining factor in selecting WMS software. Identifying the budget upfront allows for a focused search. Organizations should consider both initial costs and ongoing expenses. Some systems may have lower start-up costs but higher maintenance or licensing fees. The total cost of ownership must include factors like implementation costs, training, and support services.
Additionally, consider the return on investment (ROI) when evaluating potential software solutions. A higher initial cost may be justified if the software leads to substantial efficiency gains and cost savings over time. Careful analysis of these financial factors aids in choosing a WMS that delivers value without exceeding budget limits.
"An informed decision based on tangible requirements empowers organizations to select the most suitable WMS software, paving the way for enhanced operational success."
Throughout this exploration of factors, it becomes evident that a nuanced understanding of business size, industry requirements, and budget constraints is critical for effective WMS selection. These considerations ensure that the software fits well into the organizational framework, allowing it to adapt and grow alongside the business's evolving needs.
Leading WMS Software Solutions
The selection of an appropriate Warehouse Management System (WMS) is a critical decision for businesses engaged in logistics. With the increase in complexity in supply chains, having a strong WMS can improve operational efficiency, enhance inventory accuracy, and reduce costs. Leading WMS software solutions provide businesses with the tools they need to manage their warehouse operations effectively. This section will focus on the top solutions available in the market, dissecting their practical attributes and unique advantages.
Overview of Top Solutions
Several WMS software solutions stand out in today's marketplace. Each has its strengths tailored for different industry needs. Here are some of the most recognized options:
- SAP Extended Warehouse Management (EWM): This solution is known for its flexibility and adaptability. It integrates seamlessly with SAP's ERP offerings, making it a top choice for enterprises already using SAP software.
- Oracle Warehouse Management Cloud: Oracle's WMS is cloud-based, allowing for easy scalability. Its advanced functionalities include AI-driven insights for improved decision-making.
- Manhattan Associates WMS: This solution excels in optimizing the entire supply chain. It offers features like labor management and slotting optimization, making it suitable for large enterprises.
- Fishbowl Warehouse: Fishbowl is a popular option for small to medium-sized businesses. It provides robust inventory management features and is known for its affordable pricing.
These solutions not only vary in price and features but also cater to different business sizes and needs. Understanding these differences is key for organizations aiming to invest wisely.
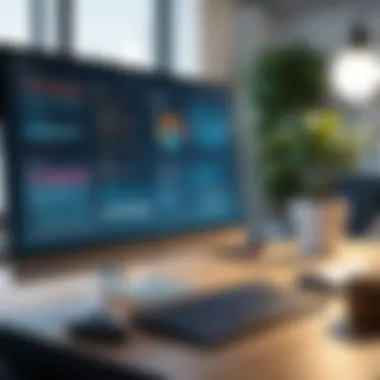

Comparative Analysis
When deciding on a WMS solution, a comparative analysis can offer insights into which system aligns best with business requirements. Some factors to consider include:
- User Interface: The ease of use of the software can significantly affect employee productivity. Some WMS solutions like Fishbowl have a more intuitive interface than others, such as SAP EWM, which may require more training.
- Cost: Budget constraints are crucial. Solutions like Fishbowl provide good value, but larger systems may offer more extensive features at a higher price. Organizations need to balance cost against functionality.
- Scalability: Cloud-based solutions such as Oracle WMS are more easily scalable than on-premise systems. This is important for businesses anticipating growth.
- Integration Capabilities: A WMS that integrates well with other business systems will save time and reduce errors. For example, Oracle WMS's capabilities to work with broader ERP solutions is a significant advantage.
These factors must be considered when evaluating the software. Each company's unique goals and challenges will determine which solution is appropriate. Consider not just current needs but also future growth and changes in technology.
"Choosing a WMS is not just about technology; it's about aligning operational capabilities with business strategy."
By conducting a thorough comparative analysis, organizations can make a well-informed decision. This, in turn, supports better warehouse efficiency and overall organizational success.
User Reviews and Testimonials
User reviews and testimonials are critical components when discussing Warehouse Management System (WMS) software solutions. They provide real-world insights into the functionality and effectiveness of the software from actual users. Positive or negative experiences shared by users can highlight both the advantages and potential pitfalls of specific systems, guiding prospective buyers towards making informed decisions.
Additionally, user-generated content fosters a sense of trust and transparency, building confidence around software choices. Businesses often rely on the experiences of their peers, as individuals in similar industries face shared challenges and requirements. Thus, harnessing these reviews can significantly impact the selection process, reinforcing the idea that authentic feedback is invaluable.
When considering WMS software, one must evaluate the credibility of the sources. Reviews should ideally come from verified users who have engaged extensively with the software. It helps to look for patterns within user feedback, as recurring themes can underline strengths or weaknesses of the software. Moreover, expert testimonials paired with user insights can also present a well-rounded view.
"User reviews provide a transparent lens into system performance, helping businesses select software that matches their operational needs."
User Experiences
User experiences with WMS software vary depending on many factors, including industry, system features, and individual business needs. These experiences provide context for the software's effectiveness in different applications. For instance, a retail business might emphasize inventory management and order fulfillment functionalities, while a manufacturing company may need robust integration capabilities.
Common themes in user experiences often include ease of use, customer support quality, and system reliability. Users frequently mention the importance of a smooth onboarding process, as it can significantly affect the overall experience. Additionally, real-time tracking capabilities often receive praise for improving operational efficiency. However, users may also highlight challenges encountered during implementation, such as integration issues with existing systems.
Case Studies
Case studies serve as valuable exemplars of how specific WMS software solutions perform in real-life settings. By analyzing these documented experiences, businesses can gain insight into the potential outcomes of using particular software. Case studies typically detail the problem faced, the implemented solution, and the subsequent results, which provide a clearer understanding of effectiveness and efficiency gains.
For example, a case study might illustrate how a logistics company adopted a specific WMS software, focusing on the automation of inventory management. The study would reveal improvement metrics such as time saved in order processing, increased accuracy in inventory counts, and reduced human error.
Such detailed accounts enable businesses to visualize potential success and challenges with their chosen WMS solution. Looking at diverse industries also encourages exploring varied applications of software, elucidating how different functionalities can address unique challenges.
By examining user reviews and case studies comprehensively, businesses gain a deeper understanding of the practical implications of WMS software, ultimately guiding informed selection.
Setting Up WMS Software
Setting up a Warehouse Management System (WMS) is a crucial process for any organization seeking to optimize its logistics operations. A well-configured WMS not only streamlines warehouse processes but also significantly improves inventory control and order fulfillment accuracy. The importance of this setup cannot be overstated; it serves as the backbone of efficient supply chain management. With a correctly established WMS, businesses can adapt more quickly to changing market conditions and maintain a competitive edge.
Implementation Steps
The implementation of a WMS involves several key steps that must be followed meticulously to ensure successful operation. Here are the primary steps:
- Needs Assessment: Identifying the specific needs of your warehouse is the first step. This involves evaluating current processes and pinpointing inefficiencies.
- Software Selection: Choose a WMS that aligns with your operational needs. Features such as scalability and integration with existing systems should be considered.
- System Configuration: This includes setting up the software according to your warehouse's requirements. Customization may be necessary to adapt the WMS to existing workflows.
- Data Migration: Transfer existing inventory and operational data into the new system. Data accuracy is crucial during this stage.
- Testing: Conduct thorough testing to ensure that all functionalities work as intended. This minimizes disruptions once the system goes live.
- Go-Live: Launch the system. It is essential to monitor the initial operation closely to address any issues that arise.
- Continuous Improvement: After implementation, ongoing evaluation and adjustment are necessary. Gather feedback and make changes to improve system performance.
Training and Support
Integrating a WMS into your operations goes beyond the technical setup; adequate training and support are equally vital. Teaching staff how to use the new system helps to facilitate a smoother transition.
Training should cover all aspects of WMS functionality, from basic navigation to advanced features. Onboarding sessions can be complemented by user manuals and online resources for continued learning. In addition to training, establishing a solid support system can mitigate challenges faced during the transition period.
Support should include:
- Helpdesk Access: A dedicated team should be available to assist users with technical issues.
- Regular Updates: Keep staff informed about software updates and new features. This ensures users can take advantage of improvements to the system.
- Feedback Opportunities: Create channels for user feedback to identify and address potential issues proactively.
Again, the role of training and ongoing support is crucial, as they create confidence among users in handling the new software. This comprehensive approach to training and support can lead to a more effective implementation of the WMS.
Challenges in WMS Software Adoption
Adopting Warehouse Management System (WMS) software is a critical move for many businesses, but it is not without its challenges. Understanding these challenges is important whether you are a small business looking to streamline operations or a large enterprise aiming to improve logistics efficiency. Acknowledging potential obstacles can help companies plan better and allocate resources more effectively.
Integration with Existing Systems
Integrating a new WMS with existing systems can be a complex process. Many organizations rely on legacy systems that were designed for different operational needs or are not compatible with modern applications. The challenge is not just technical; it also involves ensuring smooth data migration and synchronization.
The following points highlight the integration concerns:
- Technical Compatibility: Compatibility issues between the new WMS and existing software can lead to operational disruptions. Assessment of both systems before making a selection is crucial.
- Data Migration Risks: Migrating data from legacy systems carries risks. Incorrect data transfers can result in inaccuracies in inventory levels, making it essential to have a robust migration strategy.
- Business Process Redesign: Integrating a new WMS often involves redefining business processes. Staff may find it challenging to adapt, requiring attentive change management.
In some cases, it may be necessary to invest in middleware or APIs to facilitate integration with existing systems. This can add to the overall cost but is often worthwhile to ensure systems communicate effectively, leading to improved operational efficiency.
Resistance to Change
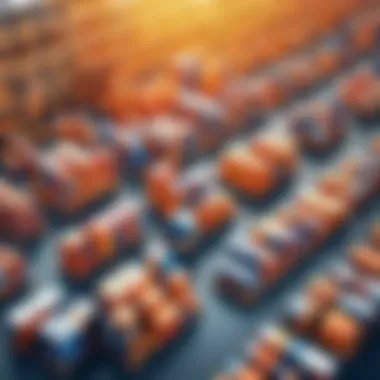

Resistance to change is a common human behavior that can hinder the successful adoption of WMS software. Employees accustomed to established methods may be apprehensive about transitioning to new processes. Such resistance can manifest in various ways: reluctance to engage with the new system, skepticism about its benefits, or even active opposition.
Key aspects of managing resistance include:
- Employee Education: Providing comprehensive training can help alleviate fears. Employees must see the benefits of the new WMS for themselves.
- Involvement in the Transition: Involving employees in the implementation process can foster a sense of ownership and reduce resistance. Gathering feedback during deployment allows staff to feel valued.
- Clear Communication: Transparent communication about the reasons for the change and expected outcomes is vital. Employees should understand how the new WMS will improve their workflows.
Successful implementation of WMS software requires fostering a culture that embraces change rather than resists it.
Organizations that manage these challenges successfully will likely find that the long-term benefits outweigh the initial hurdles. Overall, navigating the complexities of WMS adoption is an essential aspect that requires careful consideration.
Future Trends in WMS Software
The landscape of Warehouse Management System (WMS) software is rapidly evolving. Businesses recognize the importance of staying ahead in the market, and understanding future trends is vital. These trends not only shape the functionality of WMS software but also greatly influence logistics strategies across various sectors. By analyzing emerging technologies and adapting to evolving user needs, organizations can ensure that they are equipped to meet the complexities of modern supply chain management.
Emerging Technologies
In recent years, certain technologies have drastically transformed the WMS environment. One such advancement is the integration of artificial intelligence (AI) and machine learning. Organizations are using these technologies to enhance inventory accuracy and improve order prediction. The adoption of AI allows for data-driven decision making, which is critical in optimizing warehouse operations.
Automation is another key trend impacting WMS solutions. Automated systems can manage inventory tracking with higher precision and minimize errors associated with manual input. Robots in warehouses are increasingly executing tasks such as picking and packing, significantly reducing labor costs and enhancing efficiency.
Blockchain technology is gaining recognition for its ability to provide a transparent and secure method of tracking goods throughout the supply chain. This fosters trust among stakeholders and can streamline processes, especially in industries like pharmaceuticals and food, where traceability is paramount.
The Internet of Things (IoT) has become increasingly significant as well. Sensors and smart devices enable real-time monitoring of inventories, equipment conditions, and environmental factors. This real-time data can enhance responsiveness and operational agility.
Evolving User Needs
As the market grows, so do the needs of users. Businesses today require WMS solutions that are not only robust but also adaptable. Users seek systems that can effortlessly integrate with existing technologies. Scalability is crucial; organizations need solutions that can grow alongside their operations.
Furthermore, user experience has become a major focal point for WMS providers. Intuitive interfaces and easy navigation are essential factors that influence a user’s choice of software. Training and onboarding processes should also be streamlined, allowing staff to become proficient in using software quickly.
There is also an increasing demand for analytics capabilities. Companies want actionable insights from data collected by WMS systems. A focus on reporting features that provide key performance indicators in real-time has become essential. These insights not only help in optimizing current processes but also inform future strategies.
Keeping up with emerging technologies and understanding user needs will determine the success of WMS in the future.
Regulatory and Compliance Considerations
Understanding regulatory and compliance considerations is critical for any organization looking to implement Warehouse Management System (WMS) software. These considerations ensure that a business not only adheres to industry regulations but also operates within the confines of law and ethical standards. This aspect gains significance as logistics operations become increasingly complex and intertwined with global supply chains.
Navigating this landscape involves two primary components: Industry Standards and Data Protection Guidelines.
Industry Standards
Industry standards serve as benchmarks for quality, safety, and efficiency. Compliance with these standards can positively affect an organization’s reputation and operational success. In the realm of WMS, several standards may apply, depending upon the sector. Examples include the ISO 9001 standards for quality management systems and the GS1 standards for barcoding and data capture, crucial in inventory and shipment accuracy.
Achieving compliance with these standards can bring many benefits:
- Improved Operational Efficiency: Adhering to established standards often leads to streamlined processes and reduced errors.
- Enhanced Customer Trust: Meeting industry standards assures clients of the quality and reliability of services.
- Competitive Advantage: Companies that prioritize compliance can differentiate themselves in the marketplace.
Organizations must regularly review and update their WMS systems to ensure that they meet evolving standards. Moreover, participating in relevant training and workshops can help staff maintain a compliant environment.
Data Protection Guidelines
Data protection guidelines are increasingly important, especially with the rise of data-driven solutions. WMS software handles vast amounts of sensitive information, such as inventory details, customer data, and supplier agreements. Non-compliance in this area can lead to serious legal implications and potential financial penalties.
Key regulations, such as the General Data Protection Regulation (GDPR) in Europe and the California Consumer Privacy Act (CCPA) in the United States, impose strict requirements for data protection and user consent. Here are some considerations for compliance:
- User Consent: Ensure that explicit consent is obtained before collecting personal data.
- Data Encryption: Use strong encryption methods to protect sensitive information both at rest and in transit.
- Regular Audits: Conduct frequent reviews of data practices to identify and rectify compliance gaps.
To highlight the importance of these guidelines, consider this statement:
"Ignoring data protection regulations can lead to irreversible damage to an organization’s credibility and trustworthiness."
Ending
The conclusion section of this article plays a crucial role in reinforcing the significance of Warehouse Management Systems (WMS). It is where the key takeaways are summarized, thereby enabling readers to distill the dense information previously discussed into digestible insights. A well-structured conclusion not only recaps essential points but also highlights the real-world applicability of the information, ensuring that it resonates with the diverse logistical needs of businesses.
Summary of Key Insights
The section provides a recap of the important aspects presented throughout the article. First, understanding the foundational components of WMS software—such as inventory management, order fulfillment, and integration capabilities—is vital. Each feature contributes to enhancing operational efficiency, accuracy, and even cost-effectiveness. Readers should note how these systems can be tailored to meet specific industry demands through careful consideration of scalability and budget constraints.
Another critical insight is the importance of real user reviews and testimonials when selecting the right WMS software. These firsthand accounts offer invaluable perspectives that go beyond mere marketing claims. Businesses can make informed decisions only if they consider these user experiences alongside the technical specifications of each software solution.
Finally, staying aware of regulatory and compliance issues is essential for operational integrity. This aspect underscores the necessity of aligning WMS functionalities with industry standards and data protection guidelines.
Final Thoughts on WMS Selection
As the logistics landscape evolves, the selection of a WMS solution becomes an increasingly strategic decision. Businesses should approach the process with an understanding of their unique operational needs and the specific challenges they face. It is advisable to conduct thorough comparisons of different systems, weighing their respective merits against the company’s goals. Critical questions should encompass:
- How will this system integrate with existing infrastructure?
- What is the level of support and training provided by the vendor?
- Are there hidden costs beyond the initial investment?
Investing in a suitable WMS software is not merely a technical upgrade; it is a pathway to streamlined operations, improved service levels, and ultimately, enhanced customer satisfaction. By the end of this article, the reader should recognize that selecting the right WMS is a pivotal step towards achieving comprehensive logistics operations.