Implementing Quality Management Systems Successfully
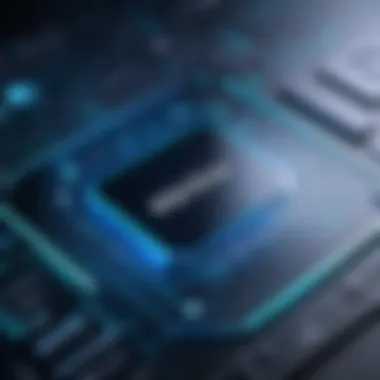
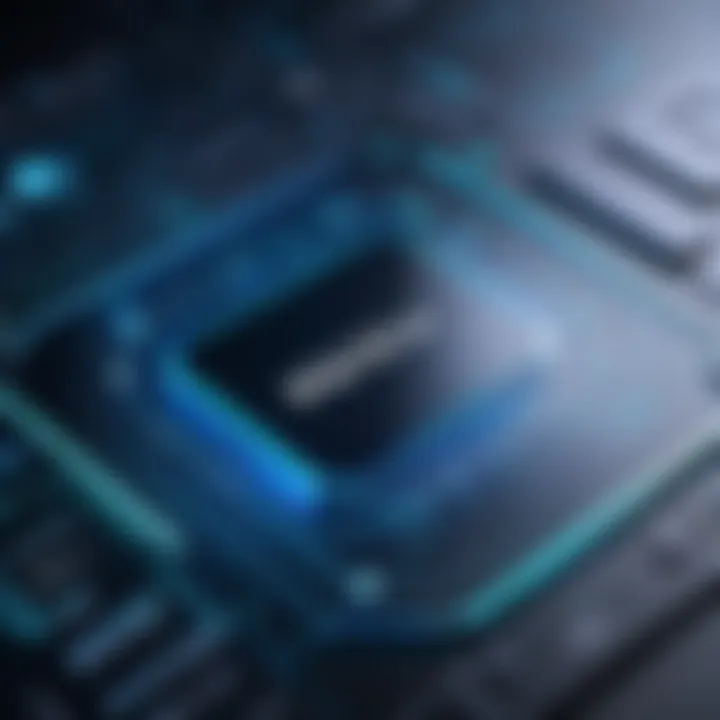
Intro
In today's competitive business landscape, organizations must adopt robust management systems to stay ahead. Quality Management Systems (QMS) serve as fundamental frameworks that guide businesses toward achieving excellence. Implementing a QMS not only enhances processes, but it also drives customer satisfaction and overall performance.
The significance of QMS lies in its ability to streamline operations while ensuring consistent quality in products and services. Organizations looking to adopt these systems need to consider various factors, including principles, implementation steps, and potential challenges. This article seeks to illuminate these crucial aspects, helping readers understand how to navigate the complexities of QMS implementation effectively.
Understanding Quality Management Systems
Quality Management Systems (QMS) are frameworks that guide organizations in their quest for quality through systematic processes and practices. Understanding the elements of a QMS is vital as they provide a strategic approach to managing quality in products and services. Implementing a QMS leads to numerous benefits including increased efficiency, enhanced customer satisfaction, and continuous improvement. Organizations that invest time in understanding these systems position themselves for greater success in a competitive landscape.
Definition of Quality Management Systems
A Quality Management System refers to a set of interrelated or interacting elements that organizations use to develop, implement, and achieve their quality policies and objectives. This includes the organizational structure, procedures, processes, and resources needed to implement quality management. A well-defined QMS ensures that an organization can consistently deliver products and services that meet customer and regulatory requirements.
Importance of Quality Management
Quality management is crucial for several reasons. It helps organizations avoid waste and inefficiencies by streamlining processes. Consistent application of quality management practices can lead to improved product quality, ultimately boosting customer satisfaction. Additionally, organizations that prioritize quality are better equipped to adapt to changing market demands and improve their competitiveness.
Key Principles of Quality Management
The key principles of quality management form the foundation of a QMS. Understanding these principles is essential for effective implementation. The principles include:
Customer Focus
Customer focus is the cornerstone of quality management. Prioritizing the needs and expectations of customers leads to higher satisfaction levels. A key characteristic of this principle is understanding customer requirements, which can drive product and service enhancements. Customer focus is beneficial because it fosters loyalty and repeat business. However, its unique feature is that it requires continuous engagement with customers, requiring time and resources.
Leadership
Leadership plays a pivotal role in establishing a quality-oriented culture. Strong leaders inspire their teams, ensuring alignment with the organization’s quality objectives. This principle is beneficial as it promotes accountability and direction. A unique feature of effective leadership in quality management is the ability to create an inclusive environment where all individuals feel valued, though it may sometimes lead to decision-making bottlenecks if consensus is not reached timely.
Involvement of People
The involvement of people refers to engaging all employees in quality management processes. When individuals at all levels participate, their diverse insights can lead to innovative solutions. This aspect is significant as it enables ownership and accountability among staff. A unique aspect of people involvement is the potential for enhanced morale and motivation, which can, however, be challenging to maintain over time if not managed well.
Process Approach
Taking a process approach involves understanding and managing interrelated processes as a system contributes to the organization's effectiveness and efficiency. This principle is beneficial as it helps organizations identify bottlenecks and areas for improvement. Its unique feature lies in the emphasis on systematic management, though it may require significant training and adaptation to existing processes.
Systematic Approach to Management
A systematic approach to management is essential in ensuring a consistent framework is followed throughout the organization. This principle is beneficial because it helps in aligning all activities with strategic objectives. A unique characteristic of this approach is its ability to provide a structured way to address quality issues, though it can be complex to implement across all departments due to varying functions and objectives.
"By aligning strategies within a QMS, organizations can ensure they are not only meeting quality benchmarks but are also capable of exceeding them."
Overall, understanding these principles is foundational to implementing an effective Quality Management System that can adapt to both the challenges and opportunities presented by the market.
Preparing for Implementation
Preparing for implementation of a Quality Management System (QMS) is crucial for organizations aiming to enhance overall quality and performance. This phase lays the groundwork for a successful rollout. It involves evaluating the current quality framework, setting clear objectives, and actively involving stakeholders. A well-prepared implementation can minimize challenges and streamline processes.
Assessing Current Quality Practices
Assessing current quality practices is the first step in preparation. It involves a thorough evaluation of existing systems, procedures, and compliance with any relevant standards. This assessment helps identify gaps in quality control and potential areas for improvement. By finding weaknesses before implementation begins, organizations can tailor their QMS to their specific needs. This proactive approach allows companies to address issues upfront, leading to a smoother transition and enhanced effectiveness of the new system.
Defining Objectives and Goals
Defining objectives and goals is necessary for the QMS implementation to align with the broader business strategy. Clear objectives guide the development of the system and provide a roadmap for progress. Organizations should establish specific, measurable, achievable, relevant, and time-bound (SMART) goals that embody both quality targets and operational excellence. Well-defined objectives foster focus and commitment from all team members, ensuring that everyone understands their role in delivering quality outcomes.
Engaging Stakeholders
Engaging stakeholders is an essential aspect of preparing for implementing a QMS. This process ensures that all parties involved, from leadership to frontline employees, are informed, involved, and committed to the change.
Identifying Key Stakeholders
Identifying key stakeholders is about pinpointing the individuals and groups crucial to the QMS. These include department heads, team leaders, quality assurance personnel, and even customers. They possess the necessary insights to shape the system effectively. One significant advantage is that key stakeholders can express their requirements and expectations, which enhances the practicality of the QMS. Additionally, engaging these stakeholders early on cultivates a sense of ownership and accountability, contributing to a smoother implementation.
Communicating the Vision
Communicating the vision for the QMS is vital to aligning stakeholders with organizational aspirations. A clear vision articulates the purpose and objectives of the QMS, inspiring all involved to rally behind a common goal. This communication should involve not just announcing the vision but fostering discussions that promote understanding. The key characteristic of this aspect is transparency, which builds trust among stakeholders. However, it can be challenging if not managed well. If the vision isn't compelling, it may lead to disengagement.
Effective preparation is the backbone of QMS implementation. Failing to engage stakeholders and assess current practices can derail the entire process.
Steps for Implementing a Quality Management System
Implementing a Quality Management System (QMS) requires a structured approach to ensure that the system meets its objectives effectively. Each step plays a critical role in laying the groundwork for enhanced quality and operational efficiency. This section explores the essential processes involved in QMS implementation, highlighting their benefits, considerations, and overall significance.
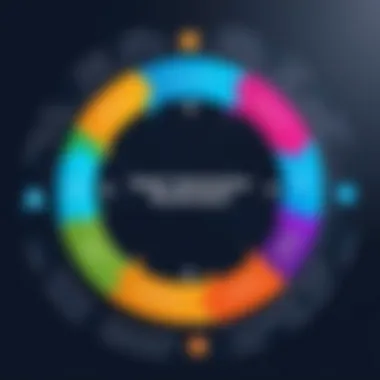
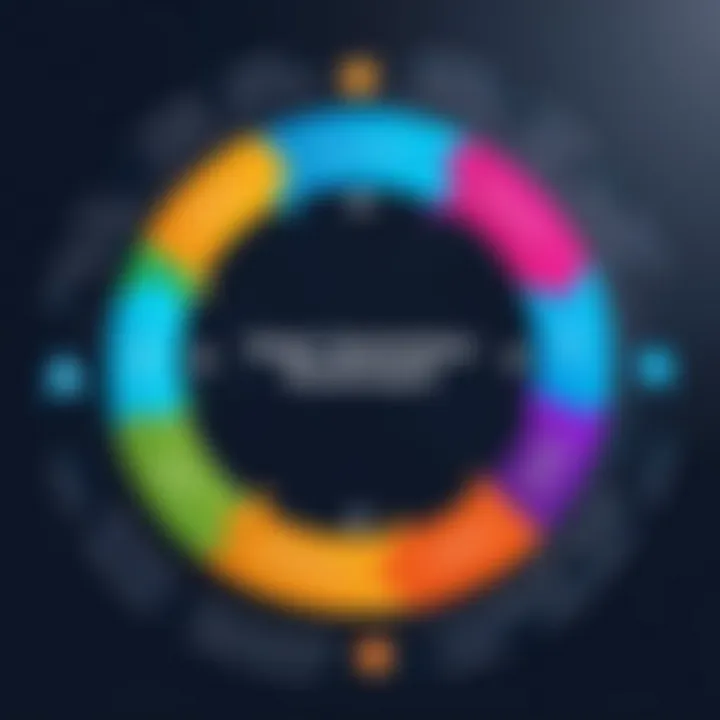
Developing a Quality Policy
A quality policy serves as a fundamental framework for a QMS. It articulates the organization’s commitment to maintaining quality standards and outlines the objectives and principles guiding quality efforts. Developing a quality policy involves identifying the mission and vision of the organization, aligning them with customer expectations, and expressing the intent to meet regulatory requirements. A clear policy fosters a sense of direction for employees and reflects the organization’s long-term dedication to quality improvements. Involving top management in crafting this policy ensures that it resonates throughout the organization, enhancing its impact.
Establishing Quality Objectives
Establishing quality objectives is crucial for measuring the success of the QMS. These objectives should be specific, measurable, achievable, relevant, and time-bound (SMART).
SMART Criteria
The SMART criteria provide a structured way to set quality objectives, ensuring clarity and focus. Each element of SMART emphasizes a different quality of the objectives.
- Specific: Objectives should be clear and precise.
- Measurable: Metrics must be established to gauge progress.
- Achievable: Goals should be realistic given the available resources.
- Relevant: They should align with broader business goals.
- Time-bound: A deadline helps maintain urgency and accountability.
Using SMART criteria is beneficial because it promotes accountability across teams. It allows for easier evaluation of whether objectives have been met, fostering continuous improvement. Moreover, the establishment of approachable goals can motivate employees, as they see tangible outcomes from their efforts.
Aligning with Business Goals
Aligning quality objectives with business goals ensures that quality efforts support overall organizational strategy. This approach prevents quality initiatives from becoming siloed and fosters collaboration across departments. Key characteristics of alignment include:
- Consistency: Ensuring that quality goals mirror overall objectives.
- Integration: Merging quality processes with operational workflows.
This alignment is advantageous as it reinforces the role of quality management as a vital component of business performance. When quality objectives are seen as integral to success, buy-in from employees and stakeholders increases. Failure to align can lead to miscommunication and wasted resources, ultimately harming both quality efforts and business performance.
Documenting Processes and Procedures
Documentation is essential for a successful QMS. Clear documentation provides a roadmap for all processes, ensuring consistency, transparency, and ease of training. All procedures should be outlined in formal documents, detailing roles, responsibilities, and steps necessary to achieve quality objectives. This documentation serves multiple purposes:
- Ensures compliance with industry regulations.
- Facilitates internal audits and assessments.
- Provides new employees with essential training materials.
Implementing Training Programs
Training programs are vital for equipping employees with the skills and knowledge necessary to uphold quality standards. These programs should be designed to cater to varying levels of experience and departments within the organization.
Identifying Training Needs
Identifying training needs involves gauging employees' current skills versus what is required to effectively implement the QMS. A thorough skills assessment helps in recognizing gaps and tailoring training programs accordingly. This practice is beneficial because:
- It allows for targeted training.
- Empowers employees with necessary knowledge.
The unique aspect of identifying training needs is that it requires collaboration across departments to ensure all perspectives are considered. This engagement can lead to more comprehensive and effective training strategies.
Delivery Methods
Training delivery methods can vary based on what best suits the organization and its employees. Common methods include online courses, workshops, and on-the-job training. Each method has its own merits:
- Online Courses: Flexible and cost-effective.
- Workshops: Interactive, fostering teamwork.
- On-the-Job Training: Immediate application of skills.
Choosing the right delivery method is essential. Effective training increases employee competence and confidence in maintaining quality standards, thus enhancing the overall QMS.
Launching the QMS
The launch of the QMS is the culmination of prior steps and requires careful planning. This stage involves communicating the new system to all employees, highlighting its importance and objectives. A structured launch helps mitigate resistance and fosters enthusiastic acceptance by presenting the QMS as a valuable asset for both employees and the organization. Addressing potential concerns early allows for smoother implementation, leading to better outcomes.
The focused implementation of each of these steps creates a robust foundation for a Quality Management System. This systematic approach ultimately elevates quality standards and contributes to the overall business performance.
Monitoring and Reviewing the QMS
Monitoring and reviewing a Quality Management System (QMS) is crucial for ensuring its effectiveness and alignment with organizational goals. This process allows businesses to assess the performance of their QMS continually. It enables them to identify areas for improvement, evaluate compliance with established standards, and enhance overall efficiency. The key lies in regular assessment and understanding of how well the system meets its objectives.
The benefits of monitoring the QMS include early detection of issues, increased customer satisfaction, and improved resource management. By systematically observing processes and outcomes, organizations can respond proactively to challenges rather than reacting to problems when they arise. Moreover, regular reviews foster a culture of continuous improvement, where employees are encouraged to seek ways to enhance quality standards.
Considerations in this process include establishing clear performance metrics, enabling open communication among stakeholders, and promoting a supportive organizational culture. These factors create an environment conducive to ongoing evaluation and adaptation in response to changing conditions or needs.
Establishing Key Performance Indicators (KPIs)
Key Performance Indicators play a significant role in monitoring a QMS. KPIs provide measurable values that gauge an organization's performance against its quality objectives. Establishing relevant KPIs is essential for tracking progress and guiding decision-making.
When selecting KPIs, it is crucial to ensure they align with the organization's strategic goals. Effective KPIs should be specific, measurable, attainable, relevant, and time-bound. This framework—often referred to as SMART—ensures that the selected indicators provide valuable insights into quality management performance.
Conducting Internal Audits
Conducting internal audits is a vital aspect of the QMS monitoring process. Internal audits help organizations evaluate the effectiveness of their quality management practices and identify areas that require improvement. The audits offer a structured way to verify compliance with regulations and internal policies.
Audit Planning
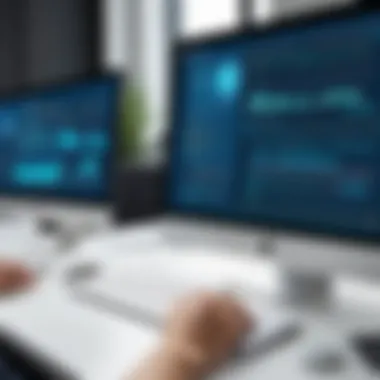
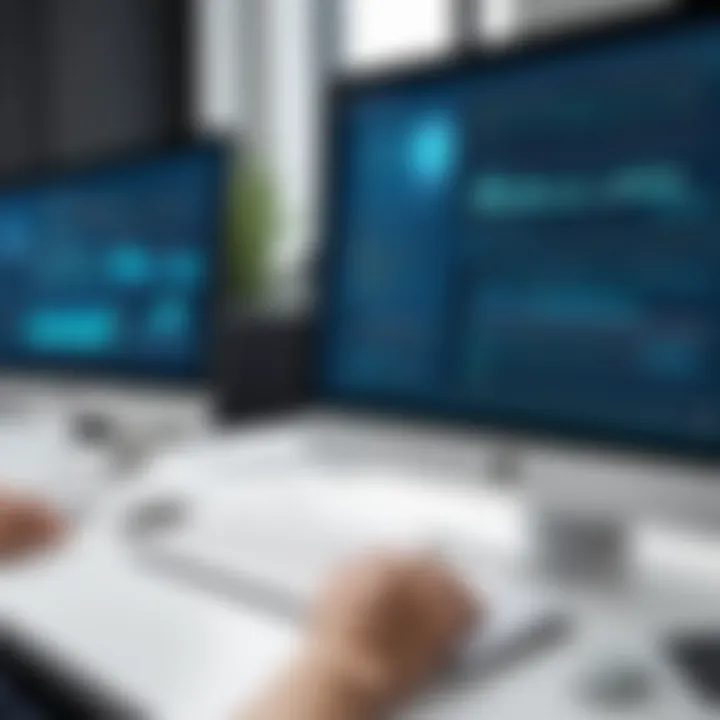
Audit Planning is a key characteristic of the auditing process. It involves outlining the scope, objectives, and resources needed for the audit. Proper planning is crucial as it sets the foundation for a thorough and effective audit. A well-executed audit plan allows organizations to utilize their resources efficiently, ensuring that the audits are not only comprehensive but also focused on the most critical areas.
Benefits of audit planning include clarity of objectives and systematic allocation of tasks. One unique feature is that it establishes a timeline, which helps avoid delays and ensures timely identification of issues. Nevertheless, the planning phase can sometimes be time-consuming and requires significant input from various stakeholders.
Reporting Findings
Reporting Findings is another important aspect of the internal audit process. Following the completion of an audit, communicating the results is essential for driving improvements. Reporting should be straightforward and focus on key observations, providing context and recommendations for action. Effective communication ensures that everyone understands the issues identified and the steps needed for resolution.
The main characteristic of reporting findings is its role in fostering transparency within the organization. A well-structured report promotes accountability and encourages employee engagement in quality management efforts. The unique feature of this process is that it serves both as an evaluative tool and as a catalyst for change. However, if not handled carefully, reporting can be met with resistance, particularly if it highlights areas needing significant adjustment.
Addressing Challenges in QMS Implementation
Understanding the importance of this topic includes recognizing that challenges can arise from internal processes, human factors, or external pressures. Each of these elements can significantly hinder the effectiveness of a QMS if not addressed properly. Organizations benefit from acknowledging these challenges, as it fosters a culture of continuous improvement and adaptability. Overall, effectively addressing challenges lays a strong foundation for a resilient and high-performing QMS.
Common Obstacles
Organizations frequently encounter various obstacles when implementing a QMS. Some of the most common issues include:
- Resistance to Change: Employees may be set in their ways or fearful of the new system, leading to pushback during the implementation phase.
- Lack of Resources: Insufficient time, personnel, or financial investment can hamper efforts to establish a comprehensive QMS.
- Poor Communication: Inadequate sharing of information regarding the QMS can create confusion and misunderstandings among stakeholders.
- Inadequately Defined Processes: Without clear process documentation, teams may struggle to adhere to the new procedures.
These obstacles can deter the successful implementation of a QMS and, if unaddressed, may lead to stagnation or regression of quality initiatives.
Strategies for Overcoming Challenges
Organizations can adopt specific strategies tailored to mitigate the challenges identified during the QMS implementation. These strategies often hinge on two key factors: leadership commitment and employee involvement.
Leadership Commitment
Leadership commitment is vital for the successful implementation of a QMS. Leaders set the tone and establish the importance of quality initiatives across the organization. A strong commitment from leadership manifests in various ways, including adequate resource allocation, setting clear expectations, and embodying a quality-focused culture.
Key characteristics of leadership commitment include:
- Visible Involvement: Leaders must actively participate in QMS activities, demonstrating their support.
- Transparent Communication: Open channels of communication about quality goals help align the organization towards a common objective.
The unique feature of leadership commitment is its ability to foster an environment where quality is prioritized, thus influencing employee attitudes positively. However, if leaders fail to show genuine commitment, the initiative may lack direction, leading to ineffective implementations and disillusioned teams.
Employee Involvement
Employee involvement is equally crucial in overcoming challenges related to QMS implementation. Engaging employees fosters a sense of ownership and motivates them to actively contribute to quality processes.
Key characteristics of employee involvement include:
- Empowerment: Giving employees the authority to influence quality practices supports innovative solutions and improvements.
- Feedback Mechanisms: Actively seeking input from employees helps identify potential challenges early in the process.
The unique feature of employee involvement lies in its potential to cultivate a participative culture, wherein staff feel valued and are more likely to embrace changes. Nevertheless, inadequate engagement can lead to frustration and diminish the overall effectiveness of QMS efforts.
In summary, addressing challenges in QMS implementation requires a comprehensive approach that emphasizes leadership commitment and employee involvement. This creates an environment of collaboration and continuous improvement, which is essential for the QMS to thrive.
Continuous Improvement in Quality Management
Continuous improvement is a cornerstone in the domain of quality management. It represents an ongoing effort to enhance products, services, or processes through incremental improvements over time. The goal of such efforts is not only to meet but exceed customer expectations, thereby ensuring higher satisfaction and loyalty.
The significance of continuous improvement lies in its multifaceted benefits. First, it fosters a culture of change within organizations. Employees become accustomed to analyzing processes critically and suggesting enhancements. This can lead to a more engaged workforce, which is essential for effective quality management. Moreover, improvement initiatives enable an organization to respond swiftly to market changes, which is crucial in today's fast-paced business environment.
Another advantage is the potential for cost reduction. By identifying wasteful practices and inefficiencies, companies can implement changes that lead to significant savings. This, in turn, can enhance profit margins and allow for reinvestment in other critical areas of the business.
In addition to cost savings, continuous improvement often leads to enhanced operational efficiency. Streamlined processes not only reduce the amount of time needed to complete tasks but can also lead to higher product quality. This is particularly important for businesses that wish to develop a competitive edge.
Lastly, an aspect to consider is the alignment of continuous improvement with organizational goals. It is imperative that the initiatives undertaken resonate with the strategic vision of the company. This alignment ensures that efforts are not just reactionary but are also forward-looking, positively influencing the overall direction of the company.
"Continuous improvement is better than delayed perfection."
– Mark Twain
The Plan-Do-Check-Act Cycle
The Plan-Do-Check-Act (PDCA) cycle is one of the most effective methods for implementing continuous improvement in quality management. The cycle includes four distinct phases:
- Plan: Identify an opportunity and plan for change. This involves gathering data, analyzing current processes, and determining what needs improvement.
- Do: Implement the change on a small scale. This helps to limit potential disruption while observing the effect of the alteration.
- Check: Monitor the results of the change. Is the new process actually achieving the desired improvement? Assessment of data is critical here.
- Act: If the change was successful, incorporate it into the wider processes of the organization. If not, analyze what went wrong and try again.
The PDCA cycle is not a one-time process but rather a repetitive sequence of steps that can be applied to different areas of the organization, thus continuously enhancing quality management practices.
Integration of Feedback Mechanisms
Feedback mechanisms are vital for the continuous improvement process. They provide the necessary insights to make informed decisions and guide future efforts. Here are some essential points on the integration of feedback mechanisms:
- Regular Surveys: Conducting employee and customer surveys can reveal areas needing improvement. This direct input can guide decision-making.
- Performance Metrics: Establishing key performance indicators allows companies to quantitatively measure the success of implemented changes.
- Suggestion Boxes: Simple, suggestion boxes can encourage employees to share ideas for improvement anonymously, fostering a culture of participation.
- Reviews and Discussions: Regular meetings to discuss feedback and improvement points can help sustain focus on quality management.
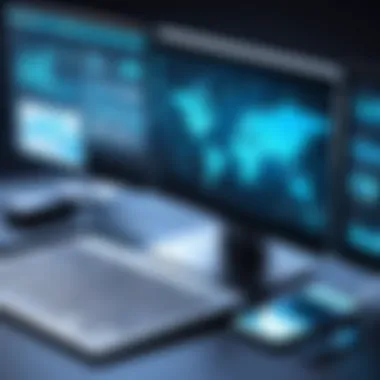
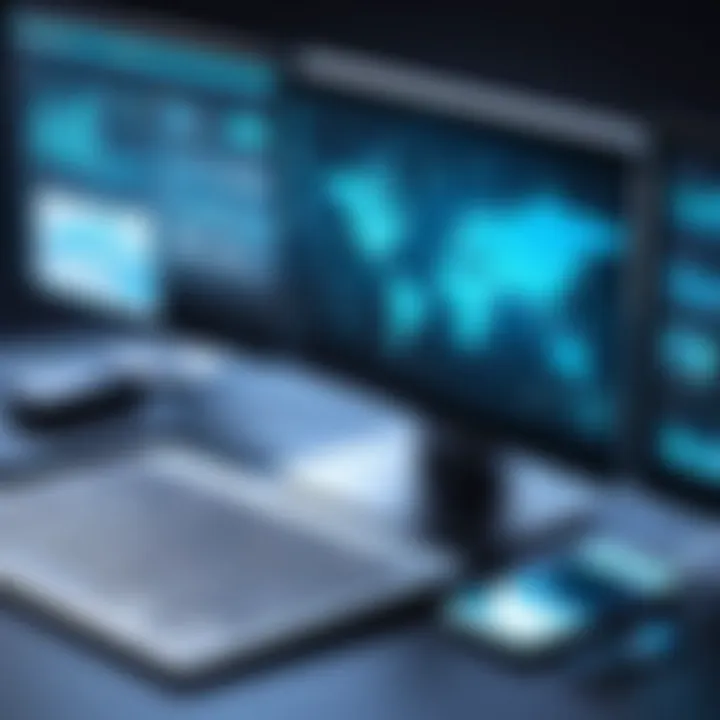
In sum, effective continuous improvement in quality management requires a structured approach, employing methods like the PDCA cycle. Feedback mechanisms strengthen this process, ensuring that organizations continuously evolve and adapt while keeping quality at the forefront.
The Role of Technology in Quality Management
In today’s fast-paced business environment, technology plays a crucial role in the efficacious execution of Quality Management Systems (QMS). The integration of advanced technological tools not only streamlines processes but also enhances the accuracy and reliability of quality data collection and analysis. It enables organizations to monitor quality in real-time, facilitating immediate corrective actions, which is vital for maintaining high standards of quality.
One significant aspect is the automation of quality processes. By utilizing software for QMS, organizations can minimize human error and increase efficiency in daily operations. This shift toward automated solutions is becoming increasingly common as companies aim to enhance their competitiveness while ensuring adherence to quality standards. Embracing technology in quality management ultimately yields cost savings and fosters a culture of continuous improvement.
Utilizing Software for QMS
Implementing specialized software for QMS provides organizations with structured frameworks that guide their quality initiatives. Such software often comes equipped with features that support documentation management, corrective actions tracking, and compliance monitoring. These tools foster collaboration among teams, making it easier to access and share quality-related information across various departments.
Moreover, software solutions can allow for the integration of quality metrics into standard reporting systems. This centralization of data not only aids in real-time decision-making but also informs strategy adjustments based on reliable insights.
Emerging Technologies in Quality Management
As quality management continues to evolve, emerging technologies are increasingly influencing practices and approaches. Two notable examples are Artificial Intelligence and Data Analytics. Both of these technologies have a profound impact in terms of how organizations manage quality processes and utilize data for strategic choices.
Artificial Intelligence
Artificial Intelligence (AI) contributes significantly to predictive analytics in quality management. By analyzing past performance data, AI can identify patterns and predict potential quality issues before they arise. This proactive approach allows organizations to implement preventive measures rather than reactive solutions when issues surface.
A key characteristic of AI is its ability to learn from new data continuously, enhancing its accuracy over time. This adaptability is a strong reason for its growing popularity in quality management. One unique feature of AI in this context is its capacity to analyze vast amounts of data quickly, providing insights that would take a human significantly longer to uncover.
However, despite its advantages, some challenges exist. The initial implementation cost of AI technologies can be high, and there may be a learning curve for employees. Despite these drawbacks, the long-term benefits often outweigh the initial challenges.
Data Analytics
Data Analytics is an essential tool for scrutinizing quality data and deriving insights that inform better decision-making. Through systematic analysis and visualization of quality data, organizations can uncover root causes of quality failures and trends that may not be evident otherwise.
The ability to present data in various formats is a noteworthy characteristic of Data Analytics. These presentations range from charts to dashboards, making it easy for stakeholders to interpret and act upon the data. This clarity in data representation is a strong reason for its utility in quality management, as it supports transparency and accountability.
Nonetheless, organizations must be cautious about data overload. Without a clear focus on relevant metrics, there is a risk of losing valuable insights in excessive information. Nevertheless, when effectively managed, data analytics can enhance quality processes and contribute significantly to organizational performance.
Case Studies and Best Practices
The significance of this section lies in its ability to ground theoretical concepts in reality. Case studies allow organizations to learn from others, avoiding past mistakes, and replicating successes. By examining the experiences of both small and large businesses, readers can discern effective practices tailored to their own unique contexts. The benefits of studying real-world implementations of QMS include gaining practical knowledge and fostering a culture of continuous learning among teams. Furthermore, these examples often discuss changes in specific metrics, offering quantitative evidence of improvements.
Another critical consideration in this context is the diversity of industries represented in these studies. Quality management is not a one-size-fits-all endeavor, and practices that work well in manufacturing may not suit the software sector. Therefore, by analyzing a variety of case studies, professionals can better understand how to adapt QMS principles to their specific needs and environments, increasing the likelihood of success.
Successful QMS Implementations
Successful QMS implementations are defined by strategic actions that align with the overall business goals. For instance, consider the case of Toyota, which is renowned for its commitment to quality through the Toyota Production System. This company has consistently demonstrated how a meticulous approach to process management directly influences efficiency and customer satisfaction. Its embrace of the concept of "Kaizen," or continuous improvement, symbolizes the ongoing nature of quality management.
Similarly, in the technology realm, companies like Microsoft have adapted QMS principles through their software development practices. By embedding quality control processes within their Agile methodologies, they have seen improved product outcomes and heightened user satisfaction. These tactical adjustments illustrate that adapting quality management to fit the operational model can yield significant benefits.
Implementations such as these also highlight the importance of employee engagement. It is not sufficient to impose new quality standards; buy-in from the workforce is crucial for success. Organizations need to invest in training and development to ensure employees understand and embrace quality practices. Regular feedback loops can sustain involvement and alignment with the organization's objectives.
Lessons Learned
Lessons learned from QMS implementations add another layer of insight into the quality management landscape. Organizations often encounter several hurdles, such as resistance to change or inadequate training, which can impede progress. A case worth mentioning is that of a healthcare provider, which faced significant setbacks after introducing a new QMS framework. Initially, a lack of clear communication led to confusion and misunderstandings among staff, resulting in low morale and ineffective adoption of the system.
However, through iterative adjustments and sustained emphasis on communication, the organization managed to realign its strategy, illustrating the significance of adaptability. This highlights an essential lesson: flexibility is as important as the initial plan. Organizations must continuously assess both their processes and the response of their teams.
Additionally, sound leadership emerged as a recurrent theme across various case studies. Leaders who actively promote a quality-centric culture and are visible in their commitment to QMS principles can inspire wider acceptance and involvement. Consequently, a focus on leadership can lead to substantial improvements in quality practices.
In summary, both successful case studies and lessons learned underscore not only the feasibility of implementing a Quality Management System but also the importance of a customized approach. Returning to key concepts and adapting methodologies based on feedback fosters an environment where quality management can thrive, ultimately leading to enhanced performance and satisfaction.
End
In the implementation of a Quality Management System (QMS), the conclusion serves as a vital anchor point. It consolidates the key learnings and reflections drawn from preceding sections, emphasizing the integral role of a QMS in driving organizational excellence. One of the principal benefits of effective QMS implementation is the enhancement of operational efficiency. Organizations, both small and large, can streamline processes, reduce waste, and optimize resource allocation. These improvements directly contribute to increased customer satisfaction, as products and services become more reliable.
Furthermore, a properly executed QMS fosters a culture of continuous improvement. This culture encourages all employees to engage proactively in quality-related initiatives, which can yield innovation and responsiveness to market changes. The conclusion should also highlight the strategic importance of setting a clear vision for quality management. This clarity helps align all stakeholders towards common goals and ensures effective communication throughout the implementation journey.
Additionally, considerations around future challenges should be noted. Uncertainties in market dynamics, shifts in consumer expectations, and evolving technological landscapes will invariably impact quality management practices. Thus, an adaptable approach, grounded in the principles of the QMS, is essential for sustaining quality standards over time.
"The journey of quality management is an ongoing process that necessitates commitment, awareness, and adaptation."
Ultimately, this conclusion underscores that implementing a QMS is not merely a one-time project. It is a significant, evolving commitment to quality that requires ongoing evaluation and enhancement. Organizations that prioritize this commitment are best positioned to achieve long-term success and heightened customer loyalty.
Summary of Key Concepts
The summary should encapsulate the critical elements discussed throughout the article on Quality Management Systems. Key concepts include:
- Understanding Quality Management Systems: This section provided a foundational grasp of what QMS entails, the importance it holds for organizations, and the key principles that guide it.
- Preparing for Implementation: It detailed the preliminary steps crucial for effective QMS deployment, such as assessing current practices and stakeholder engagement.
- Steps for Implementing a Quality Management System: This included practical guidance on establishing a quality policy and launching training initiatives, influencing the QMS's success.
- Monitoring and Reviewing the QMS: This highlighted the importance of KPIs and audits, ensuring that the system remains effective and relevant.
- Addressing Challenges in QMS Implementation: The discussion of obstacles and strategies for overcoming them emphasized the essence of leadership and employee involvement in reinforcing quality culture.
- Continuous Improvement in Quality Management: Focused on the significance of iterative processes and feedback mechanisms, empowering managers to refine quality practices.
- The Role of Technology in Quality Management: Explored how modern tools, like data analytics, assist organizations in enhancing quality controls.
- Case Studies and Best Practices: These provided real-world examples illuminating the successful application of QMS principles.
Future Directions for QMS
Looking forward, the evolution of Quality Management Systems will likely encompass several vital aspects:
- Integration of Artificial Intelligence: AI can play a transformative role in analyzing data and predicting trends, enabling organizations to act swiftly on quality insights.
- Remote Quality Management Solutions: Remote work changes the landscape. Organizations will need to adapt their QMS strategies to manage quality in a decentralized environment.
- Sustainability Considerations: As businesses increasingly focus on sustainability, QMS frameworks will need to integrate environmental considerations into their quality objectives.
- Enhanced Training Approaches: The nature of training programs may evolve to incorporate more virtual learning tools and methods, fostering greater participation across diverse teams.
- Increased Collaboration Across Industries: The future will likely see businesses collaborating on best practices for QMS, particularly in sectors that face common challenges.