Manufacturing Quality Management: Principles & Practices
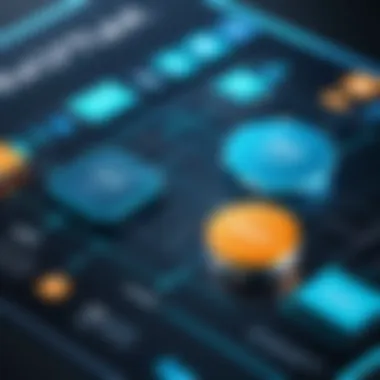
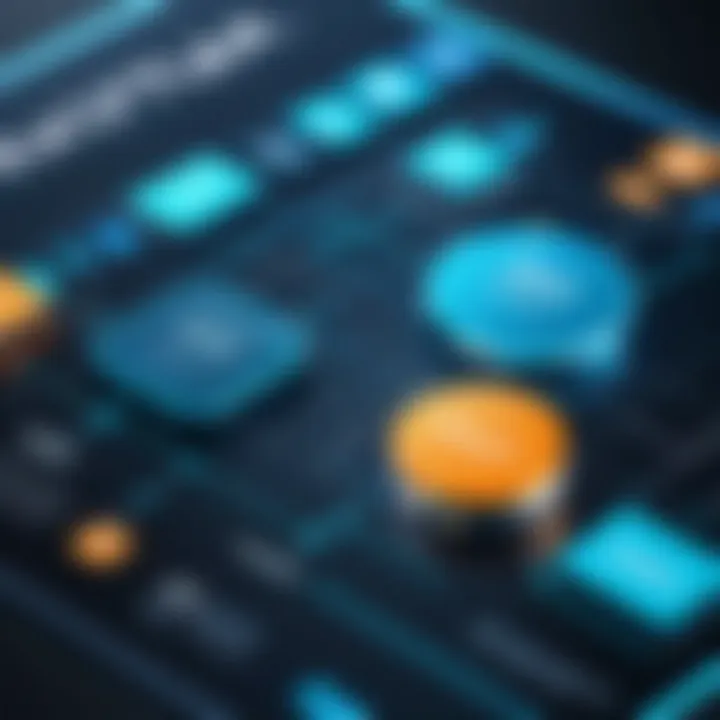
Intro
Manufacturing quality management is a vital discipline that intersects various principles and methodologies. Its core goal is to ensure that products meet specified quality standards while improving operational efficiency. Understanding this domain requires a deep dive into its key components and the practices that makes it effective.
In today’s fast-paced environment, organizations need to prioritize quality not just for compliance, but to gain competitive advantage. By exploring the principles and best practices of manufacturing quality management, stakeholders can adopt strategies that enhance overall productivity and product excellence.
Key Features and Benefits
Overview of Features
Manufacturing quality management encompasses several essential features:
- Principles of Quality Management: These are foundational beliefs that guide quality practices within an organization.
- Methodologies: Different approaches such as Total Quality Management (TQM) and Statistical Process Control (SPC) help streamline processes.
- Tools and Technologies: Advanced tools like Six Sigma and Lean Manufacturing play a significant role in identifying waste and improving efficiency.
- Regulatory Compliance: Understanding legal standards is crucial to maintaining product quality and safety in manufacturing.
Benefits to Users
The benefits of implementing effective quality management practices are manifold:
- Improved Product Quality: Ensures that the end products consistently meet or exceed quality standards, leading to higher customer satisfaction.
- Operational Efficiency: Streamlining processes reduces waste, promoting better resource management.
- Cost Reduction: Effective quality management can lead to lower defect rates, minimizing costs associated with rework and returns.
- Risk Mitigation: Proactive quality management helps identify potential issues before they escalate, reducing the risk of product failures.
"Quality is not an act, it is a habit."
— Aristotle
Comparison with Alternatives
Head-to-Head Feature Analysis
Exploring alternative approaches can provide insights into the effectiveness of various quality management strategies. For instance, comparing Lean Manufacturing and Six Sigma reveals distinctive focuses:
- Lean Manufacturing specializes in minimizing waste.
- Six Sigma concentrates on reducing defects.
Each method's suitability depends on specific manufacturing needs and goals.
Pricing Comparison
While Assessing costs can vary significantly based on the chosen methodology and tools, the investment in quality management systems often yields significant returns. By weighing the potential ROI against initial expenses, organizations can make informed decisions that align with their strategic goals.
Understanding Manufacturing Quality Management
Manufacturing quality management is pivotal in today’s industrial landscape. It refers to systematic processes to ensure products meet specific standards and customer expectations. The significance of manufacturing quality management cannot be overstated. It directly impacts operational efficiency, customer satisfaction, and business reputation. A structured and effective approach can lead to reduced waste, lower costs, and higher quality standards that distinguish a company in competitive markets.
Quality management encompasses several vital elements. Firstly, it involves clearly defined strategies that guide quality assurance practices. Secondly, a deep understanding of customer needs is essential; it helps businesses align their processes with market demands. Finally, continuous assessment and adaptation allow organizations to respond to changes swiftly.
Thus, understanding manufacturing quality management aids organizations in achieving operational excellence. It fosters a culture of quality and encourages engagement across all levels of a company. This section lays the foundation for exploring more detailed principles, best practices, and methodologies in subsequent sections.
Definition and Scope
The term "manufacturing quality management" encapsulates a wide range of concepts. At its core, it is about overseeing and guiding quality assurance processes from product conception through production and delivery. The scope includes various aspects such as quality planning, quality control, quality assurance, and quality improvement. Each of these areas serves distinct functions yet collectively contributes to achieving comprehensive quality management.
Quality planning involves establishing quality objectives and the processes needed to attain them. On the other hand, quality control focuses on measuring and monitoring production processes to ensure quality standards are met. Quality assurance sets the framework within which quality processes operate, while quality improvement is about continuous assessment and enhancement of systems, processes, and products.
In doing so, manufacturing quality management ensures that products not only meet legal and regulatory requeriments but also satisfy customer expectations and enhance business performance.
Historical Development
The practice of quality management has evolved significantly over the decades. Early manufacturing relied on basic quality control procedures, often reducing defects through manual inspections. This approach was reactive, addressing issues only after they occurred.
The introduction of statistical techniques in the mid-20th century marked a significant shift. Pioneers such as W. Edwards Deming and Joseph Juran highlighted the importance of proactive quality management. They encouraged organizations to adopt processes that focus on preventing defects rather than merely detecting them. This mindset laid the groundwork for modern quality management systems.
In the late 20th century, the global marketplace began to pressure companies to improve quality further. This led to the implementation of quality standards such as ISO 9000 series. These standards provided a framework for creating effective quality management systems.
Today, quality management in manufacturing combines traditional methods with advanced technologies, such as automation and data analytics. This evolution reflects a growing recognition of the need for quality in building consumer trust and enhancing operational efficiency.
Key Principles of Quality Management
The principles of quality management serve as a foundational framework for organizations seeking to enhance their quality practices. By understanding these principles, companies can better align their operations to meet customer expectations, improve operational efficiency, and ensure consistent product quality. In this section, we explore three key principles: customer focus, continuous improvement, and engagement of people, each of which plays a critical role in driving successful quality management practices.
Customer Focus
A primary principle of quality management is a strong emphasis on customer focus. This aspect centers on understanding and meeting the needs of customers in all facets of production. It recognizes that the ultimate goal of any manufacturing process is to deliver products that satisfy customer requirements and expectations.
To effectively implement this principle, organizations must engage in several key activities:
- Gather Feedback: Regularly collect customer feedback through surveys, reviews, and direct interactions. This data forms the basis for quality assessments and improvements.
- Set Clear Goals: Define clear quality objectives based on customer expectations. These goals should guide decision-making processes across all departments.
- Involve Customers in the Design Process: When possible, customers should be included in the product design phase to align features with their needs.
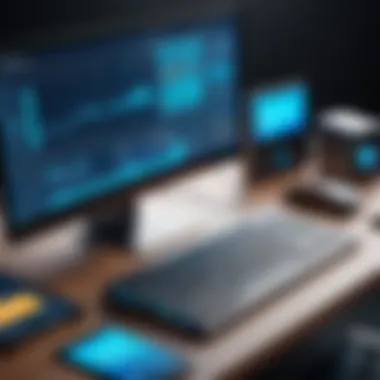
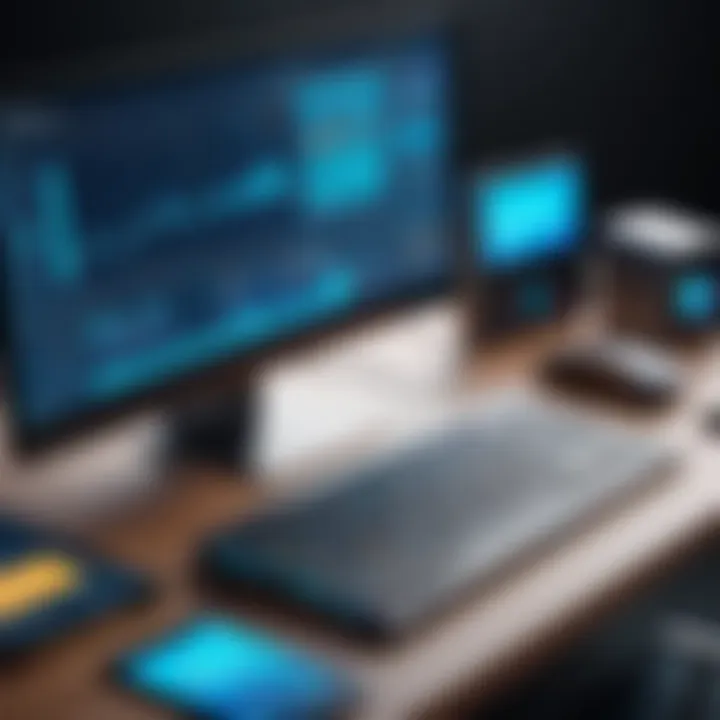
The benefits of a customer-focused approach are substantial. Companies that prioritize their customers tend to achieve higher satisfaction rates, foster brand loyalty, and enhance their reputation within the market. This principle is not just about reacting to customer needs but proactively anticipating them, making it essential in today's competitive landscape.
Continuous Improvement
Another vital principle in manufacturing quality management is continuous improvement. This involves ongoing efforts to enhance products, services, or processes. Rather than being a one-time effort, continuous improvement is a culture that organizations embrace.
Employing continuous improvement requires:
- Adopting Methodologies: Systems such as Lean and Six Sigma offer structured approaches to identify inefficiencies and reduce waste while enhancing product quality.
- Data-Driven Decision Making: Utilizing data analytics to identify areas for improvement is crucial. Companies should embrace tools that facilitate tracking and analyzing performance metrics.
- Employee Engagement: Employees at all levels should be encouraged to suggest areas for improvement, fostering a culture where everyone contributes to enhancement efforts.
Continuous improvement not only leads to better quality but also drives cost efficiencies. This ongoing commitment helps organizations stay relevant and adapt to changing market demands, propelling them towards long-term success.
Engagement of People
The principle of engagement of people highlights the importance of involving employees at all levels in quality management initiatives. Quality is not solely the responsibility of management; it requires the dedicated participation of everyone in the organization.
Key practices for fostering engagement include:
- Training and Development: Providing employees with the necessary skills and knowledge to understand quality standards helps them contribute effectively.
- Empowering Employees: Granting employees the authority to make decisions regarding quality can lead to quicker resolutions of problems and foster a sense of ownership.
- Promoting Collaborative Work Environments: Encourage teamwork across departments to solve quality-related issues and share best practices.
An engaged workforce is typically more innovative, productive, and committed to enhancing quality standards. By empowering individuals to take part in quality management, organizations create a culture that values improvement and results in better overall performance.
"The quality of a leader is reflected in the standards they set for themselves."
By focusing on these key principles, organizations can create a solid foundation for quality management. In doing so, they not only meet but exceed customer expectations, paving the way for successful and sustainable operational practices.
Quality Management Systems in Manufacturing
The implementation of Quality Management Systems (QMS) in manufacturing is pivotal for organizations striving to achieve consistent product quality and operational effectiveness. These systems create a structured approach to managing processes, ensuring compliance with regulatory standards and enhancing customer satisfaction. By adopting such systems, manufacturers can significantly reduce defects and improve overall efficiency.
Quality Management Systems are not just a regulatory requirement; they are vital for minimizing waste, lowering costs, and improving competitiveness in the marketplace. They provide a framework that allows organizations to clearly define their quality objectives, implement processes to meet these objectives, and regularly assess and improve these processes over time.
ISO Standards
ISO
ISO 9001 is a fundamental standard that outlines the criteria for a quality management system. It is widely recognized and applies to any organization, irrespective of its size or industry. This standard emphasizes a process approach to quality management, focusing on providing products that meet customer requirements and enhance satisfaction. One of its key characteristics is its flexibility, allowing businesses to tailor their processes to meet specific needs and regulatory requirements.
The unique feature of ISO 9001 is its focus on continual improvement and customer satisfaction, making it a beneficial choice for manufacturers looking to establish a robust quality management culture. However, the implementation can be resource-intensive and may require an initial investment in staff training and adjustments to existing processes.
ISO/TS
ISO/TS 16949 is a technical specification that aims to improve quality in the automotive industry. It integrates the requirements of ISO 9001 with additional automotive-specific requirements, creating a comprehensive framework for manufacturers. A critical characteristic of this standard is its focus on defect prevention and waste reduction.
ISO/TS 16949's unique feature is its alignment with the automotive industry's specific needs, which provides distinct advantages in achieving high levels of quality assurance. However, the complexity of the standard and the specific industry focus can also pose challenges for manufacturers who may find it difficult to align their existing processes with its stringent requirements.
Six Sigma
DMAIC Methodology
The DMAIC methodology is a core component of the Six Sigma framework, serving as a systematic approach for improving processes. It stands for Define, Measure, Analyze, Improve, and Control. Each stage of the DMAIC process provides detailed guidance on how to identify and eliminate defects in manufacturing processes.
A key characteristic of this methodology is its emphasis on data-driven decision making, which allows organizations to focus on critical areas that need improvement. This feature makes DMAIC a highly effective tool for achieving quality management objectives. However, its successful implementation requires a commitment to training personnel and collecting accurate data.
Benefits of Six Sigma
The benefits of Six Sigma extend beyond mere defect reduction; it encompasses financial savings, improved customer satisfaction, and enhanced productivity. One of its notable characteristics is its potential to transform organizational culture towards continuous improvement and accountability.
The unique feature of Six Sigma’s benefits lies in its comprehensive approach to quality management, which combines technical tools and employee engagement. Nevertheless, organizations may face challenges in adopting Six Sigma if there is resistance from staff or if adequate resources are not allocated to training and development.
Lean Manufacturing
Principles of Lean
Lean manufacturing principles focus on maximizing value while minimizing waste. This approach helps manufacturers streamline their operations and optimize resources. A key characteristic of lean principles is the belief that any process that does not add value should be eliminated.
The unique feature of lean manufacturing is its emphasis on continuous improvement through incremental changes. This aspect can lead to significant long-term gains in operational efficiency. Conversely, the transition to a lean approach can require significant changes in mindsets and practices, which may meet resistance from employees.
Lean Tools
Lean tools such as value stream mapping, 5S, and kaizen are essential for implementing lean principles in manufacturing environments. These tools are designed to identify inefficiencies and enhance process flow. The main characteristic of these tools is their focus on creating a culture of improvement and engagement at all levels of the organization.
The unique feature of lean tools is their practical application in real-world settings, enabling rapid adoption and integration into daily operations. However, organizations might face challenges in consistently applying these tools, especially in complex manufacturing environments that resist change.
Tools and Techniques for Quality Management
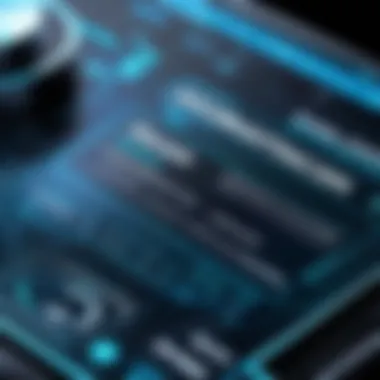
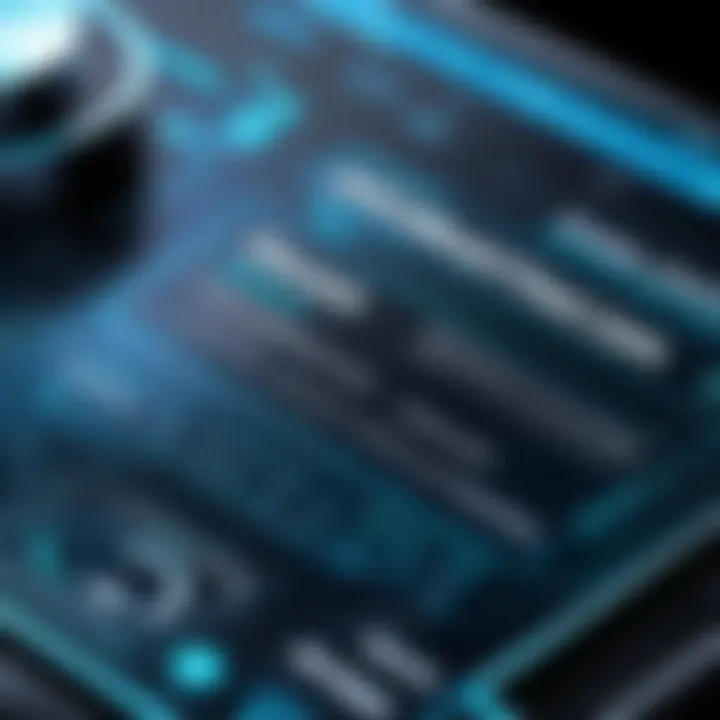
The success of any manufacturing operation hinges on effective quality management. This not only ensures that products meet customer expectations but also boosts operational efficiencies. The right tools and techniques offer a systematic approach to managing quality effectively. Understanding these components can significantly enhance decision-making processes and lead to better business outcomes.
Statistical Process Control (SPC)
Statistical Process Control (SPC) plays a crucial role in monitoring and controlling manufacturing processes through statistical methods. By using control charts and other data visualization tools, manufacturers can identify variations in production processes early. This proactive approach reduces waste and minimizes defects.
The application of SPC allows organizations to maintain consistent quality in their products. It emphasizes the importance of processes rather than solely focusing on end results. For businesses, the benefits include:
- Early detection of process variations
- Improved consistency in product quality
- Cost savings through reduced waste
Implementing SPC requires proper training and understanding of statistical data. Without accurate data collection and analysis, the effectiveness of SPC diminishes significantly.
Failure Mode and Effects Analysis (FMEA)
Failure Mode and Effects Analysis (FMEA) is a systematic methodology for evaluating processes to identify potential failures and their impact. By forecasting potential issues, manufacturers can take preventive actions before failures occur.
FMEA enhances product reliability and safety, proving to be invaluable during the design and development phases of a product's lifecycle. The steps involved include:
- Identifying potential failure modes
- Assessing the effects of each failure
- Prioritizing the failure modes based on their risk
Through this procedure, manufacturers can focus their resources on preventing the most detrimental failures. This structured approach ultimately leads to better quality products while increasing customer satisfaction.
Root Cause Analysis
Root Cause Analysis (RCA) delves into understanding the fundamental causes of defects or problems in the manufacturing process. Rather than treating the symptoms, RCA aims to eradicate the source of the issue. This not only solves the immediate problem but also prevents its recurrence.
Key steps in conducting RCA include:
- Collecting data about the issue
- Identifying the root causes
- Developing and implementing corrective actions
- Monitoring the effectiveness of the changes
RCA can employ various methods, including the "5 Whys" and fishbone diagrams, allowing teams to visualize problems effectively. Focusing on underlying causes ensures that resources are used efficiently to maintain high standards of quality in manufacturing processes.
"Quality is never an accident. It is always the result of intelligent effort."
The Role of Technology in Quality Management
The integration of technology in quality management is imperative. In today’s fast-paced manufacturing environment, organizations must leverage advanced tools to maintain high standards of quality. Technology not only aids in precision but also enhances consistency across processes. By automating various tasks and employing sophisticated software, manufacturers can mitigate human error and boost overall efficiency.
Furthermore, technology enables real-time tracking and monitoring of production processes. This adaptability is crucial for identifying issues promptly and ensuring that products meet specified quality criteria. As manufacturers strive for excellence, the role of technology becomes a pivotal component of quality management strategies.
Automation Tools
Automation tools serve as a backbone for effective quality management. They streamline routine processes, minimizing the need for manual intervention. This reduces not only the likelihood of errors but also the time required for quality checks. Utilizing automation helps in consistently producing products that meet quality standards.
Some notable benefits of automation tools include:
- Increased Efficiency: Automation speeds up processes, allowing for faster production cycles.
- Cost Reduction: By reducing the necessity for excessive labor, companies can save money in the long run.
- Scalability: Automation can easily adapt to shifting production demands without compromising quality.
The choice of automation tools must be aligned with specific operational requirements. For example, tools like robotic process automation (RPA) can enhance repetitive tasks, while automated inspection systems can improve product evaluation.
Quality Management Software
Quality management software is essential in the landscape of technological advancements. These software solutions facilitate comprehensive data collection and analysis regarding quality metrics. They provide functionalities for tracking non-conformances, managing documentation, and ensuring compliance with regulatory standards.
Several key features of quality management software include:
- Data Centralization: They aggregate information from various processes into one interface, simplifying access to data.
- Reporting Tools: Advanced reporting features enable manufacturers to generate insights, aiding in informed decision-making.
- Audit Management: Quality management software helps in planning and executing internal audits, ensuring compliance.
For effective implementation, organizations should consider software platforms such as MasterControl or ETQ Reliance, which cater specifically to the needs of quality management in manufacturing environments.
Quality Management Challenges in Manufacturing
In the realm of manufacturing, quality management holds critical significance. Successfully navigating this field requires an awareness of various challenges that may arise. Understanding these obstacles can lead to better strategies, improved processes, and ultimately, enhanced product quality. Below, we examine two major challenges: compliance issues and resistance to change.
Compliance Issues
Compliance issues present a significant hurdle within manufacturing quality management. Regulations often come from multiple governing bodies, including local, national, and international standards. Companies must align their processes with these regulations to avoid legal penalties and maintain customer trust.
Important aspects to consider include the following:
- Variability in Standards: Different regions may have distinct regulations. A production facility operating in multiple locations may find itself challenged by varying compliance requirements.
- Documentation: Ensuring proper documentation is essential for compliance. Failure to maintain accurate records can lead to audits which might result in penalties.
- Cost of Compliance: Meeting compliance standards often requires investment in training, processes, and technologies. This can put a strain on budgets, particularly for small manufacturers.
Effectively addressing compliance issues requires continuous monitoring of regulations and proactive strategies. Companies can benefit from implementing comprehensive training programs, dedicating resources to stay informed about changes, and incorporating regulatory checks into their quality management systems.
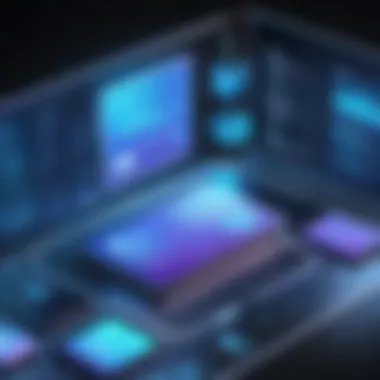

Resistance to Change
Resistance to change is another prevalent challenge within manufacturing quality management. The manufacturing sector, traditionally rooted in established processes, often displays reluctance toward new practices and technologies.
Factors contributing to resistance include:
- Cultural Inertia: Established teams may be comfortable with existing processes, leading to reluctance in adopting new methods.
- Fear of Disruption: Employees might be concerned that new changes will disrupt their roles or lead to a loss of efficiency.
- Insufficient Training: A lack of training on new systems can breed uncertainty, making staff hesitant to embrace change.
To overcome resistance, organizations should focus on fostering an adaptive culture. Communication plays a key role. Leaders must explain the benefits of changes and ensure that employees feel included in the process. Furthermore, providing adequate training can mitigate fears and foster acceptance, ensuring a smoother transition to new practices or technologies.
"Quality is never an accident; it is always the result of high intention, sincere effort, intelligent direction, and skillful execution; it represents the wise choice of many alternatives."
Best Practices for Effective Quality Management
Effective quality management is pivotal in manufacturing. Best practices in this area not only enhance product quality but also improve operational processes. They contribute to higher customer satisfaction and lower costs of production. Understanding and implementing these practices offers significant advantages for businesses.
Employee Training and Development
Investing in employee training and development is a cornerstone of quality management. Knowledgeable employees are more capable of identifying defects and suggesting improvements. Quality training programs equip personnel with the necessary skills to meet standards.
- Continuous Learning: Manufacturing techniques and customer expectations change. Regular training sessions help employees stay updated with trends.
- Skill Diversification: Encouraging cross-training among employees promotes flexibility. Workers can adapt to various roles, allowing for smoother workflow transitions.
- Enhanced Engagement: When employees are trained, they feel valued. This boosts morale and decreases turnover rates, significantly affecting the quality of work.
Prioritizing employee training leads to a more competent workforce, directly impacting a company’s quality objectives.
Monitoring and Measurement
Monitoring and measurement are essential in maintaining quality standards. Relying on data helps organizations identify trends and assess performance. By implementing effective monitoring systems, manufacturers can make informed decisions.
- Key Performance Indicators (KPIs): Establish KPIs for various processes. They provide measurable values that can indicate how well the processes are performing against the goals.
- Real-Time Data Collection: Utilize technology for real-time data. This helps in prompt identification of any quality issues before they escalate.
- Feedback Mechanisms: Regular feedback from employees and customers can reveal insights. Actively seeking this information helps to highlight areas needing attention.
Effective quality monitoring not only identifies issues but also facilitates continuous improvement.
A robust monitoring and measurement framework provides the foundation for consistent quality management. It allows a company to react swiftly and effectively to any deviations in quality levels.
Case Studies of Quality Management in Action
Understanding case studies in quality management is essential. They provide real-world examples of how principles and methodologies are applied in manufacturing settings. These case studies give insights into both successful implementations and the lessons learned. By examining these cases, organizations can identify best practices and potential pitfalls. This allows them to adapt strategies fitting their unique contexts.
Successful Implementations
Successful implementations of quality management can vary across different manufacturers. Key examples often illuminate the effectiveness of specific methodologies. For instance, Toyota's adoption of Lean Manufacturing principles exemplifies how efficiency and waste reduction can lead to significant improvements in product quality. Their production system focuses on continuous improvement, highlighting the importance of employee engagement.
Another notable example is General Electric's utilization of Six Sigma methodologies. By systematically identifying and eliminating defects, GE has been able to enhance both product quality and operational efficiency. The training of employees in the DMAIC framework empowered them to contribute meaningfully to quality initiatives. Such examples provide a roadmap for best practices.
Key factors contributing to successful implementation include:
- Strong Leadership Commitment: Top management must prioritize quality.
- Employee Involvement: Engaging all levels of the workforce is crucial.
- Training: Providing sufficient education on methodologies enhances efficacy.
These aspects create a culture that supports quality management at every level.
Lessons Learned
Case studies also reveal valuable lessons about quality management. For instance, resistance to change can hinder quality initiatives. Many organizations face challenges when introducing new processes or technologies. Understanding employee concerns and involving them early in the process can mitigate this issue.
One lesson from multiple case studies is the significance of data. Companies often overlook the role of data analytics in quality management. Data-driven decisions can help identify problem areas before they become significant issues.
Moreover, companies must be prepared for setbacks. Quality management is an iterative process. As noted in various case studies, not every initiative will yield immediate success, and it’s essential to learn and adapt.
Future Trends in Manufacturing Quality Management
Future trends in manufacturing quality management are crucial for understanding how the industry evolves, especially in today's fast-paced environment. As businesses strive to improve their operational efficiency and product quality, it becomes essential to address the cutting-edge developments that shape these dynamics. The integration of advanced technologies, sustainable practices, and innovative strategies drive significant benefits, including enhanced customer satisfaction and competitiveness.
Sustainability Initiatives
Sustainability initiatives represent an emerging focal point in manufacturing quality management. These efforts address the growing concerns related to environmental impact and social responsibility. Adopting sustainable practices enhances a company's brand image and aligns with consumer expectations for eco-friendly products.
Benefits of incorporating sustainability initiatives include:
- Resource Efficiency: Implementing sustainable processes often leads to reduced waste and optimized resource use. This efficiency not only cuts costs but also lowers the environmental footprint.
- Regulatory Compliance: Manufacturers face increasing scrutiny from regulators regarding environmental practices. Proactive sustainability measures can ensure compliance and mitigate potential penalties.
- Market Differentiation: Companies recognized for their sustainable practices can distinguish themselves in a crowded marketplace, appealing particularly to eco-conscious consumers.
However, the transition to sustainable practices requires careful planning. Organizations need to evaluate their current processes, set measurable sustainability goals, and train employees to embrace these changes. Engaging stakeholders throughout this process also fosters a culture of sustainability within the organization.
Artificial Intelligence and Machine Learning
The application of artificial intelligence (AI) and machine learning (ML) within manufacturing quality management is revolutionizing the way businesses approach quality control and process optimization. These technologies facilitate better decision-making by analyzing vast amounts of data and providing predictive insights.
Key considerations include:
- Predictive Quality Maintenance: By analyzing historical data and real-time information, AI can identify patterns that lead to defects. This allows organizations to address potential issues before they escalate, thereby preventing costly disruptions.
- Enhanced Process Optimization: Machine learning algorithms can optimize manufacturing processes by predicting equipment failures, optimizing schedules, and adjusting settings for maximum output.
- Real-Time Monitoring: AI tools can provide instant feedback on production quality, allowing teams to respond promptly to deviations from standards.
Incorporating AI and ML requires significant investment in technology and training. However, the long-term benefits of improved quality, efficiency, and cost savings justify these enhancements. By staying abreast of these technological advancements, manufacturers can maintain a competitive edge while ensuring superior product quality.