Top Mechanical Design Software for Engineers 2023
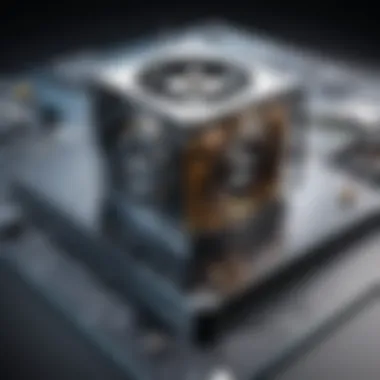
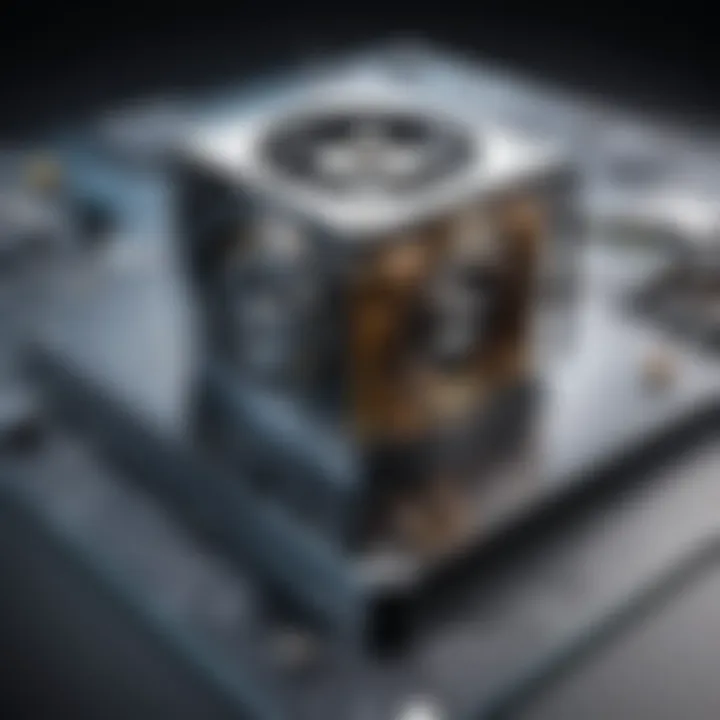
Intro
In todayโs fast-paced engineering landscape, the choice of mechanical design software can significantly impact overall productivity and innovation. This guide aims to dissect the essential aspects that define leading mechanical design software solutions. Engineers need tools that not only foster creativity but also ensure practicality in design processes.
Understanding features, usability, pricing, and how these tools fit within various industries is crucial for professionals. This exploration provides insights into software that can streamline operations and enhance the design experience. It also emphasizes the importance of making informed decisions when selecting software, given the variety of options on the market. As we dive deeper into specific applications, we will analyze different user reviews and expert opinions, supplying a comprehensive resource for both individual engineers and businesses.
Prelude to Mechanical Design Software
The field of engineering relies heavily on mechanical design software. These tools are integral to simplifying complex design processes, enhancing accuracy, and facilitating innovation. As industries evolve, the role of effective software becomes increasingly vital. Professionals must keep pace with technological advancement to maintain a competitive edge. Understanding this aspect of design software is not merely an academic exercise; it has direct implications for project efficiency and product quality.
The Importance of Mechanical Design Software
Mechanical design software provides essential capabilities that streamline workflows. It allows designers to visualize concepts in 3D, conduct simulations, and manage data efficiently. Such tools foster collaboration among team members, which can significantly improve communication during projects. This software reduces the chances of error, which can be costly and time-consuming to rectify. Without effective design tools, organizations may struggle with manual processes that often lead to inefficient designs and wasted resources.
The integration of advanced features such as generative design and finite element analysis means that engineers can make informed decisions quickly. These capabilities empower users to explore multiple design alternatives swiftly, significantly cutting down design cycles. This aspect is particularly relevant for industries where speed to market is crucial.
Evolution of Mechanical Design Tools
The journey of mechanical design tools shows a clear transition from basic drafting techniques to sophisticated software solutions. Initially, engineers relied on manual methods. These rigid processes often led to design limitations and errors, causing setbacks.
With the development of Computer-Aided Design (CAD) in the 1960s, the landscape began to change. Early CAD tools introduced electronic drawing capabilities but lacked advanced functionalities. Over decades, CAD systems evolved significantly, incorporating simulation capabilities and user-friendly interfaces.
By the late 20th century, integrated software solutions became available. Products like SolidWorks and AutoCAD evolved to combine drafting, modeling, and simulation in one platform. This integration marked a turning point. Designers now had comprehensive tools at their disposal, enabling them to tackle complex projects with ease.
Today, the use of cloud-based software and artificial intelligence is beginning to influence mechanical design. This shift signifies another evolution, with tools that adapt to user behavior and enhance collaboration even further. It highlights how mechanical design software is continually adapting to meet the varied needs of professionals in engineering and design fields.
Criteria for Selecting Mechanical Design Software
Selecting the appropriate mechanical design software is a pivotal step in ensuring successful engineering projects. Several key criteria must be evaluated to make an informed choice. These elements influence not only the productivity of design teams but also the overall quality of the final product.
User Interface and Experience
A user-friendly interface is essential for maximizing efficiency. Engineers often work under tight deadlines, making the ease of navigation and accessibility of tools within the software critical. A well-designed interface minimizes the learning curve, allowing professionals to focus on their design tasks rather than struggling with complex software menus. The balance between functionality and simplicity is crucial.
Sketching features need to be intuitive. Drag-and-drop options, customizable toolbars, and context-sensitive help can enhance user experience significantly. Feedback from users frequently highlights the importance of ergonomics in design software. Choosing software with an interface designed with engineers in mind can enhance productivity.
Functionality and Features
The functionality of mechanical design software determines its applicability across different project requirements. Key features to look for include 3D modeling capabilities, simulation tools, and collaborative features. Software that supports parametric modeling allows for modifications without starting from scratch, which can save time and resources. Additionally, simulation features help identify potential issues before physical prototypes are built, reducing errors and costs.
When exploring features, consider the specific needs of your industry. A software package that excels in automotive design may not meet the stringent requirements of aerospace projects. Therefore, identifying vital features relevant to your niche is key to selecting the right tool.
Integration with Other Tools
In todayโs fast-paced engineering environments, software integration is crucial. Most projects require the collaboration of various software tools, such as Project Management Software, Customer Relationship Management, or specialized simulation tools. A mechanical design software that offers robust API support or built-in integrations with commonly used tools can streamline workflow.
Integration enhances data sharing among departments, reducing the chances of discrepancies between designs and specifications. Additionally, it facilitates teamwork by allowing diverse teams to collaborate on a common platform. Therefore, while assessing software options, examine their integration capabilities with other essential tools you currently use.
Cost and Licensing Models
Cost is often a significant barrier when selecting mechanical design software. Various licensing models exist, including perpetual licenses, subscription models, and pay-as-you-go options. Each model has its advantages and disadvantages based on your organizationโs budget and needs.
Subscription models may seem less burdensome upfront, but costs can accumulate over time. Conversely, while perpetual licenses require a higher initial investment, they often result in lower long-term costs if the software remains in use for many years. Furthermore, consider the hidden costs associated with implementation and training, as these can substantially influence the overall expenditure.
"The right mechanical design software can transform design processes, enhancing both collaboration and efficiency.โ
In summary, the selection of mechanical design software should be guided by an assessment of user interface quality, functionality, integration capability, and cost. These criteria collectively ensure that the software not only meets current demands but also adapts to future challenges.
Overview of Leading Mechanical Design Software
In exploring mechanical design software, it is fundamental to understand the landscape. The variety in software can influence productivity and innovation in engineering. Each software solution offers unique features, usability aspects, and capacity for integration. By examining these elements, professionals can better navigate the options available and select the most suitable tools for their needs.
Benefits include:
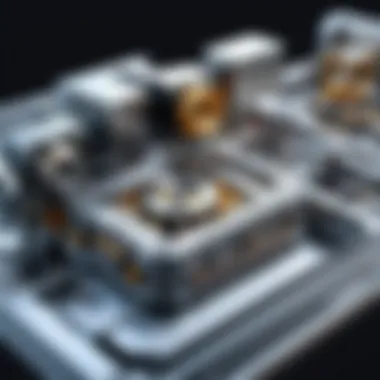
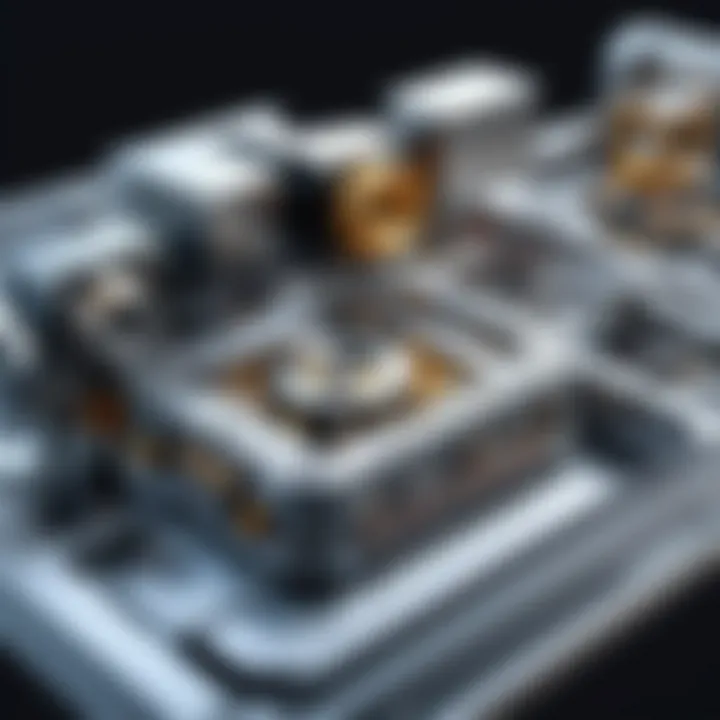
- Efficiency in design processes
- Enhanced collaboration among teams
- Capability to tackle complex engineering challenges
This overview will provide insight into notable software choices such as SolidWorks, AutoCAD, CATIA, Fusion 360, and PTC Creo, outlining their core functionalities and suitability for different applications.
SolidWorks
Key Features
SolidWorks is distinguished by its parametric feature design, allowing users to create complex geometries with precision. The assembly capabilities facilitate management of intricate assemblies, which is vital for engineering projects. Furthermore, SolidWorks integrates simulation tools that help validate designs early in the process. This contributes directly to reducing errors and optimizing performance before physical prototypes are constructed.
User Reviews
Users frequently highlight SolidWorks' intuitive interface which streamlines the design workflow. Many consider it an excellent choice for both beginners and experienced users. The community around SolidWorks fosters growth through forums and shared resources, providing a supportive environment for learning and troubleshooting. However, some reviews note that licensing costs can be a concern for smaller businesses.
Industry Applications
SolidWorks finds application in various sectors including automotive, aerospace, and consumer goods. Its versatile toolset makes it effective in designing everything from components to entire systems. Notably, many educational institutions also leverage SolidWorks for teaching purposes, underlining its importance in training the next generation of engineers.
AutoCAD
Key Features
AutoCAD is well-known for its 2D and 3D drafting capabilities. One of its key characteristics is its versatile set of tools for precision drawing and documentation. Users appreciate the ability to create highly detailed plans and layouts, which is crucial in fields like architecture and civil engineering. Its compatibility with various file formats adds to its flexibility, enabling broader usability across different projects.
User Reviews
Feedback from users indicates that AutoCAD remains a reliable solution, often praised for its robust functionality. However, some users express frustration with its learning curve. Advanced features can be overwhelming for those without prior experience. Yet, the extensive resources and tutorials available online help mitigate this issue for new users.
Industry Applications
AutoCAD is widely used in architecture, engineering, and construction. Its precise drafting tools are essential for creating blueprints and technical drawings. This software is also popular among interior designers, landscape architects, and other professionals needing detailed visual representations of their concepts.
CATIA
Key Features
CATIA is recognized for its advanced surface modeling capabilities. Its robust design tools cater to industries with complex geometrical requirements like aerospace and automotive. A notable feature is its ability to simulate product performance in real-time, allowing for comprehensive testing before production. This can significantly reduce the costs associated with physical prototyping.
User Reviews
Users report that CATIA is powerful but requires a significant investment in training. Its complexity can be a barrier for less experienced users, yet the depth of its capabilities is often deemed worth the effort. CATIA is appreciated for its ability to handle large projects and facilitate collaboration among multiple stakeholders.
Industry Applications
With its strong focus on innovative design, CATIA is a favored tool in aerospace, automotive, and high-tech industries. The collaborative aspects of CATIA support large teams working on complex projects, making it ideal for enterprises where integration among design, engineering, and manufacturing is critical.
Fusion
Key Features
Fusion 360 offers cloud-based functionality, allowing users to design, engineer, and collaborate seamlessly. Its integration of CAD, CAM, and CAE tools in a single platform is a significant advantage. The flexibility and scalability of Fusion 360 make it suitable for both individual professionals and larger teams working on complex projects.
User Reviews
Users appreciate the low entry cost compared to other professional software. The cloud features allow easy access to designs from anywhere, which enhances teamwork. Some have mentioned minor performance issues with large assemblies, but overall, user sentiment leans towards satisfaction due to its adaptability.
Industry Applications
Fusion 360 serves a broad range of industries, including product design and mechanical engineering. It is also gaining traction among hobbyists and educators, reflecting its capacity to fit diverse needs. Its approach to integrating different aspects of design and manufacturing positions it well for future growth as industries evolve.
PTC Creo
Key Features
PTC Creo is known for its parametric and direct modeling capabilities. It also excels in advanced manufacturing processes, which are increasingly important for modern engineering solutions. Users highlight its robust simulation tools that allow for detailed analysis of product designs, assisting in making data-driven decisions.
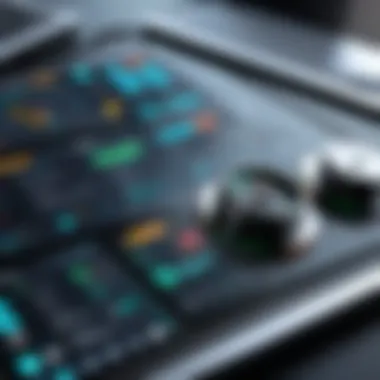
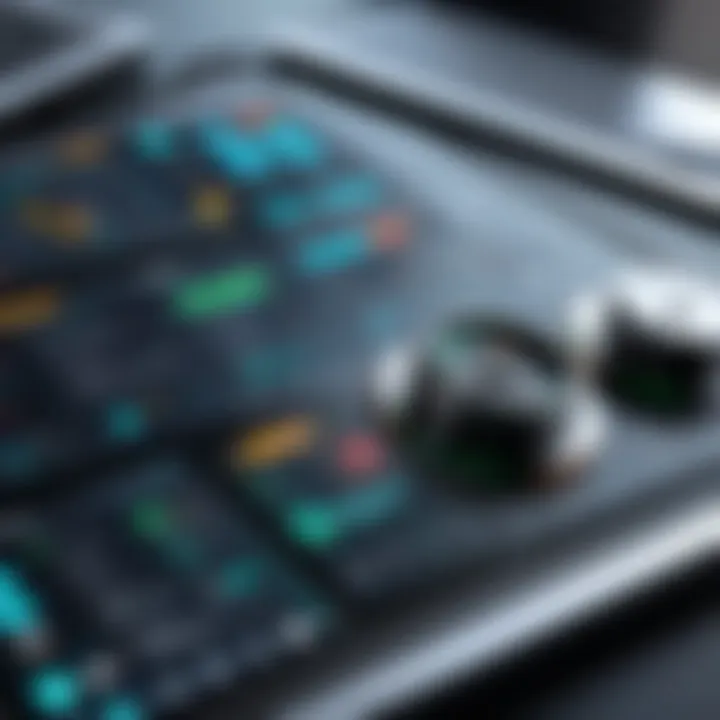
User Reviews
Many users find Creo to be comprehensive and capable, although it can be intimidating due to its steep learning curve. Experienced users note that once mastered, its potential becomes evident. The continuous updates and improvements from PTC help maintain its relevance, but the cost remains a consideration for smaller enterprises.
Industry Applications
PTC Creo is primarily used in manufacturing, electronics, and consumer products. Its features cater to companies seeking to optimize their product development processes. The flexibility to adapt to different industrial needs makes it a valuable tool in fast-paced environments where innovation is crucial.
Comparative Analysis of Top Software
The comparative analysis of mechanical design software is critical for professionals seeking to optimize their design processes. By examining the various software options available, users can better understand how different programs perform across several dimensions, such as functionality, usability, and pricing. This analysis allows engineers, designers, and businesses to make informed choices that align with their specific needs and project requirements.
In the current landscape, where design efficiency and cost-effectiveness are paramount, a robust comparison can reveal strengths and weaknesses of each tool, guiding professionals toward a solution that enhances productivity and meets their design goals.
Functionality Comparison
Functionality remains a core consideration when evaluating mechanical design software. Each software package comes with its own suite of features tailored for different types of design work. Some tools, like SolidWorks, offer advanced simulation capabilities, while others may focus more on drafting and 2D design, such as AutoCAD.
When examining functionality, users should consider the following:
- CAD Capabilities: Does the software provide sufficient tools for both 2D and 3D modeling?
- Simulation and Analysis: Are there options for stress testing or fluid dynamics simulations?
- Customization Options: Can the software be tailored to fit specific project needs?
- Collaboration Features: How well does the software support team-based projects?
This comparison helps users identify which software can handle their project demands, making it a foundational aspect of the overall analysis.
Usability Comparison
Usability is equally important. A tool that is difficult to navigate or less intuitive will hinder productivity, regardless of its capabilities. Thus, evaluating usability is essential to ensure seamless integration into existing workflows. Important factors to consider include:
- User Interface Design: Is the layout clean and easy to understand?
- Learning Curve: How long does it take for users to become proficient?
- Support Resources: Are tutorials and customer support readily available to assist users?
- User Feedback: What do real users say about their experiences with the software?
A thorough usability comparison ensures that the chosen software will not only meet technical requirements but also be user-friendly, enabling effective design work.
Pricing Comparison
Finally, pricing structures greatly influence software selection. Many design software packages have various licensing models, which include subscription fees, one-time purchases, and tiered pricing based on features. Assessing pricing involves looking into:
- Initial Costs: What is the upfront investment required?
- Recurring Fees: Are there ongoing subscription costs?
- Value for Money: Does the software provide enough features to justify its cost?
- Available Discounts or Offers: Are there promotions for beginners or educational institutions?
This pricing comparison is crucial for businesses, as it affects budgetary considerations and overall return on investment.
In summary, a comparative analysis allows professionals to navigate their options effectively, ensuring that the mechanical design software chosen aligns closely with their needs and operational context. By focusing on functionality, usability, and pricing, users can make strategic decisions that support their design ambitions.
Future Trends in Mechanical Design Software
The landscape of mechanical design software is continually changing. Factors such as technology advancements, market needs, and user feedback drive the evolution in this field. Understanding emerging trends is crucial for all stakeholders involved in design processes. Engineers and designers who recognize these trends will enhance their productivity and maintain a competitive edge.
Collaboration Features
In todayโs interconnected world, collaboration has become a key component of effective mechanical design. Software solutions now include features that allow teams to work together in real-time, regardless of their physical location. This capability is especially important for large projects, which often involve cross-disciplinary teams. For example, tools within software like SolidWorks and CATIA enable multiple users to access and modify design files simultaneously.
Benefits of these collaboration features include:
- Enhanced Communication: Users can share ideas and feedback instantly.
- Streamlined Workflows: Reduces the chances of errors resulting from version control issues.
- Improved Productivity: Teams can make quicker decisions based on immediate input from colleagues.
"Real-time collaboration improves not only speed but also the overall quality of the design."
The growing trend towards integrating communication tools shows no sign of slowing down. As time progresses, we can anticipate even more robust collaborative capabilities, including virtual reality environments.
Cloud Computing Integration
The integration of cloud computing into mechanical design software is reshaping how companies store and access data. Rather than relying solely on local servers or desktop solutions, more firms are adopting cloud solutions. With cloud-based software, accessibility becomes more flexible. Teams can work remotely while having instant access to the necessary resources.
Key advantages of cloud computing integration include:
- Greater Accessibility: Designers access files anytime, anywhere, facilitating remote work.
- Scalability: Businesses can scale their software solutions according to their project needs without significant investments.
- Cost-Effective Solutions: Reduces the need for extensive hardware and maintenance.
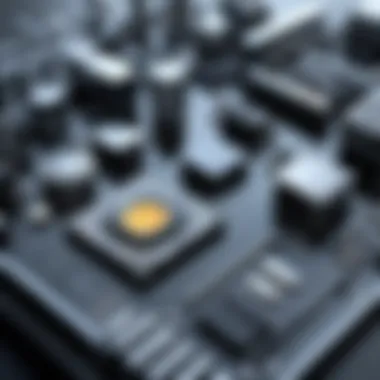
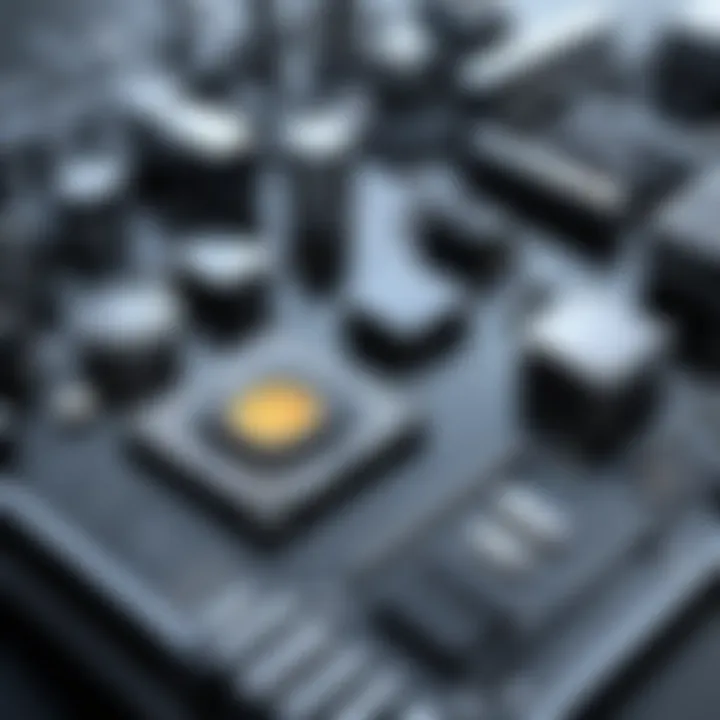
This trend is likely to continue as businesses focus on cost-efficiency and collaboration. As the technology evolves, cloud security and faster processing speeds will become critical topics within this domain.
Artificial Intelligence in Design
Artificial Intelligence is revolutionizing many industries, including mechanical design. AI systems can analyze vast amounts of data much faster than humans. This analysis leads to optimized design processes and quicker decision-making. AI can assist in various tasks such as resource allocation, simulation, and predictive analytics.
Some benefits of incorporating AI into mechanical design software are:
- Design Automation: AI-driven tools can automate mundane tasks, allowing designers to focus on creativity.
- Enhanced Simulation: AI can improve the accuracy of simulations, leading to better outcomes.
- Data-Driven Insights: AI analyzes historical designs to recommend improvements.
The growing use of AI in software indicates a shift toward more intelligent design systems. As these technologies become more refined, mechanical design software will continue to evolve, pushing the boundaries of what's possible in design methodology.
User Experiences and Testimonials
User experiences and testimonials play a crucial role in evaluating mechanical design software. They offer firsthand insights into how software performs in real-world settings. Such testimonials often highlight not just technical features but also practical usage scenarios, making them invaluable for potential users. When professionals assess various options, they seek evidence from users who have navigated similar challenges. Thus, user opinions can significantly influence software selection.
Experiences shared by users often cover several key aspects, including:
- Ease of Use: Users frequently discuss how intuitive the software interface is. A user-friendly design can streamline workflow and reduce training time.
- Performance: Testimonials often detail system reliability and speed, critical for fast-paced engineering environments.
- Support and Community: Users may emphasize the value of customer support and a solid community forum, as these can be lifesavers during problem-solving.
- Integrations: Users discuss how well the software integrates with other tools, enabling a smoother workflow across various platforms.
In addition to individual experiences, collective user testimonials can provide trends. For instance, consistently positive feedback on user support may indicate a company's commitment to customer satisfaction. Conversely, recurring complaints could signal potential issues worth considering.
"User feedback is not merely anecdotal; it can serve as a robust indicator of a product's strengths and weaknesses in practical applications."
Evaluating these testimonials allows businesses to make informed decisions while aligning their specific needs with the software capabilities.
Case Studies from Various Industries
Case studies effectively showcase how different mechanical design software performs across diverse sectors. Industries such as automotive, aerospace, and consumer products often require tailored solutions, and examining specific case studies can illuminate their unique requirements.
For instance, in the automotive industry, the use of SolidWorks has been critical in the development of complex parts. Engineers in this sector highlight how its simulation features allow for better design optimization, leading to enhanced performance and safety in vehicles.
In aerospace, CATIA is frequently featured due to its robust capabilities in handling large assemblies. Many case studies show how major manufacturers utilize its advanced functionalities to model, simulate, and fabricate components of aircraft.
On the other hand, small manufacturers might share case studies on Fusion 360, showcasing its affordability and accessibility. Feedback from these users often illustrates the balance of robust features with a lower entry cost, making it appealing to startups and small businesses.
These examples highlight that selecting software is not merely about features but understanding how those features are applied in real-world scenarios.
User Feedback Analysis
User feedback analysis involves synthesizing the insights gathered from various reviews and testimonials to identify patterns and derive actionable conclusions. For mechanical design software, this analysis sheds light on user satisfaction, performance efficiency, and potential areas for improvement.
Structured feedback often considers specific metrics and characteristics:
- Rating Systems: Many platforms employ user rating systems. Average ratings can give a quick overview of software performance and satisfaction.
- Common Themes in Reviews: Analyzing numerous reviews reveals commonly praised features, such as collaboration tools or cloud integration, and frequently criticized aspects like customer support delays.
- Quantitative vs. Qualitative Insights: Unlike numerical ratings, qualitative feedback provides context. Users sharing detailed stories about their successes or frustrations give depth to the ratings.
It's essential to assess this feedback objectively and consider the broader context. Some users may have unique expectations or challenges not representative of the general user base. By examining this feedback critically, organizations can understand how software meets broader industry needs and individual preferences.
Overall, user experiences and testimonials create a feedback loop that helps not only potential users in choosing appropriate tools but also developers in refining their products.
Epilogue
In the complex world of mechanical design, the right software plays a pivotal role. This conclusion summarizes the key points discussed throughout the article while also offering insights into making informed decisions about mechanical design software. Understanding the features and functionalities of leading software is vital. This allows users to select tools that align with their unique needs and industry requirements.
Selecting mechanical design software requires careful consideration of various elements. Each software has strengths and weaknesses, and understanding these can lead to better outcomes in design processes. Additionally, user experience and integration with other tools are crucial. This makes it easier to implement and use these designs in real-world applications. By analyzing user feedback and expert reviews, this article offered a frame of reference for users considering new software solutions.
Investing in the proper software is an investment in efficiency and innovation.
Summarization of Key Points
The article covered several essential topics regarding mechanical design software, including:
- Key Features: Each software's unique capabilities were discussed, shedding light on what makes them stand out.
- User Experience: Ease of use fosters better productivity among users, which is critical in meeting project deadlines.
- Industry Applications: Different industries have varying requirements, and selecting software tailored to specific needs is crucial.
- Cost and Licensing Models: Cost-effectiveness is a vital factor. Choosing the software that provides the best value for money can lead to substantial savings in the long run.
This comprehensive approach underscores the importance of deliberate selection based on the discussed attributes.
Final Recommendations
- Evaluate Needs Carefully: Assess your team's specific requirements before choosing any software. Consider factors such as the complexity of projects and compatibility with existing tools.
- Trial Versions: Whenever possible, use demo versions or trials to gain firsthand experience of the software's interface and capabilities. This practical exposure can greatly aid in the decision-making process.
- Gather Feedback: Collect input from team members who will use the software regularly. Their opinions will provide valuable insights.
- Consider Future Needs: Think about long-term needs and software scalability. A solution that fits your current needs may not serve you well as your responsibilities expand.
- Stay Updated: The field of mechanical design software is constantly evolving. Regularly check for updates in software solutions to take advantage of new features and enhancements.
By keeping these recommendations in mind, professionals can enhance their design processes and achieve greater efficiency in their projects.