Understanding Computer Aided Manufacturing: Concepts and Applications
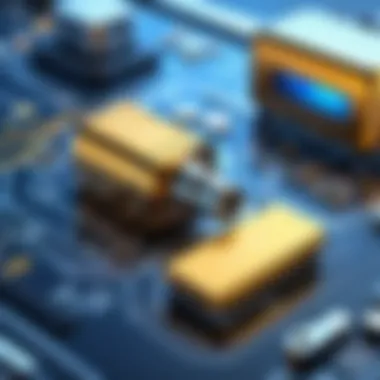
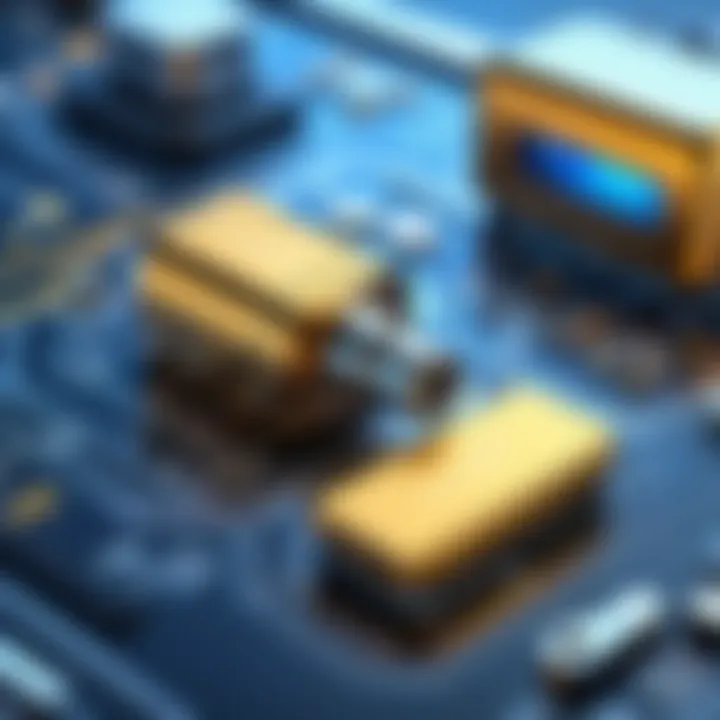
Intro
Computer Aided Manufacturing (CAM) has become a cornerstone in modern production settings. It leverages technology to enhance the efficiency and precision of manufacturing processes. Many industries incorporate CAM to streamline operations, reduce human error, and promote overall productivity. This exploration of CAM not only highlights its significance in today's manufacturing landscape but also sheds light on how it integrates with design and engineering processes.
As companies face increasing competition, the demand for improved quality and reduced turnaround times has driven a shift towards automation. Consequently, understanding the concepts and applications of CAM is essential for professionals navigating this rapidly evolving field. This article aims to provide insights into the intricacies of CAM, from its core features to the benefits it offers, and the challenges it presents for implementation.
Key Features and Benefits
Overview of Features
One of the most notable features of CAM is its ability to facilitate complex manufacturing tasks that would be challenging to execute manually. CAM systems utilize advanced software to generate precise tool paths, optimize production schedules, and manage resources more efficiently.
- Automation of Processes: CAM systems allow for the automation of machining processes. This reduces manual intervention and enhances safety.
- Flexibility: CAM can quickly adapt to design changes, allowing for customized production without extensive downtime.
- Integration: CAM software can work seamlessly with CAD (Computer Aided Design) systems, ensuring that design data flows efficiently through the manufacturing process.
Benefits to Users
Utilizing CAM leads to several substantial benefits for companies, regardless of their size or industry sector.
- Increased Efficiency: CAM enhances production speed, enabling manufacturers to respond rapidly to market demands.
- Higher Quality Products: The precision achieved through CAM reduces quantifiable errors, resulting in high-quality outputs.
- Cost Reduction: The automation and optimization capabilities of CAM can lead to significant cost savings over time, making it a financially viable option.
"CAM plays a vital role in transforming traditional manufacturing into smart factories where efficiency and adaptability are key."
Comparison with Alternatives
Head-to-Head Feature Analysis
When comparing CAM to traditional manufacturing methods, the differences are substantial. Traditional methods often rely heavily on manual labor and manual processes, leading to variability in quality and longer lead times. On the other hand, CAM systems ensure consistency and precision.
- Speed: CAM can execute tasks much quicker than manual processes, especially in repetitive tasks.
- Accuracy: Automation diminishes the risk of human errors commonly found in manual settings.
- Data Utilization: CAM operates on data analysis, utilizing historical production data to improve future processes.
Pricing Comparison
The initial cost of implementing CAM can be high due to the required software and equipment investments. However, many users find that the return on investment is favorable when considering the long-term efficiency gains and cost reductions. Traditional methods, while less expensive upfront, often incur higher costs due to inefficiencies and error correction.
Preface to Computer Aided Manufacturing
Computer Aided Manufacturing, commonly known as CAM, plays a crucial role in the modern manufacturing landscape. It integrates technology and manufacturing processes through software and hardware systems. By automating production, CAM enhances precision, speed, and efficiency. This section emphasizes why understanding CAM is vital for IT professionals, software developers, and business operators in both small and large enterprises.
The importance of CAM extends beyond mere machinery operation; it fundamentally transforms how products are designed and produced. Manufacturers benefit from increased output rates and reduced variability, leading to fewer errors in production. By minimizing human intervention, errors are reduced significantly, yielding a more reliable manufacturing process.
CAM systems facilitate various manufacturing techniques like milling, turning, and laser cutting. Each of these methods requires precise programming and control, which CAM software provides. Furthermore, this integration fosters continuous improvement methodologies, such as lean manufacturing, which aim to eliminate waste and optimize processes.
Several key elements underline the significance of CAM:
- Automation of Processes: CAM automates repetitive tasks, reducing labor costs and human errors.
- Customization Capabilities: CAM allows for easy modifications in production settings, adapting to various design requirements.
- Data-driven Decision Making: CAM systems can analyze production data, assisting in better decision-making processes.
Moreover, considerations around cost and training can impact the implementation of CAM technologies. While initial investments may be steep, the potential for cost savings and increased revenue through improved productivity justifies this expense over time. Companies must also ensure their workforce is trained on CAM systems to fully harness the technology's advantages.
In summary, understanding Computer Aided Manufacturing is integral for anyone involved in production or design. As industries evolve and the demand for high-quality products increases, CAM stands out as a tool that aligns technological capabilities with manufacturing needs.
"The integration of CAM systems is no longer optional; it is essential for maintaining competitiveness in today's manufacturing environment."
Historical Development of CAM
The historical development of Computer Aided Manufacturing (CAM) is a crucial subject in understanding its current applications and significance in the manufacturing landscape. Recognizing its evolution helps professionals grasp the technological advancements that have shaped how industries operate today. By examining milestones in this evolution, one can appreciate the role of CAM in streamlining processes, improving productivity, and enhancing precision throughout production environments.
Early Innovations
The roots of CAM can be traced back to the introduction of numerical control (NC) machines in the 1940s and 1950s. These innovations laid the groundwork for modern manufacturing technologies. Originally, NC machines used punched tape to control machine tools. This technique represented a significant shift from manual operation to automated processes, allowing for greater accuracy and consistency in machining tasks.
One pertinent example is the development of the first NC machine by John T. Parsons and his team, utilizing a punched card to execute precise movements. This innovation signaled the dawn of computer assistance in manufacturing, heralding a new era wherein machines could operate under pre-programmed instructions.
Evolution through the Decades
As technology progressed, so too did the CAM systems. In the 1960s, computers began to play a more significant role in manufacturing. The introduction of computer numerical control (CNC) systems took the automation concept further. With CNC, programming became more sophisticated, as operators could input complex geometric data, leading to designs and products that were once difficult or impossible to create.
During the 1970s, the emergence of Computer Aided Design (CAD) systems greatly impacted CAM. The capability to design using software facilitated a seamless transition from design to production. CAD systems provided high-level visualization tools for designers, allowing for adjustments and optimizations before the fabrication phase.
In the 1980s and 1990s, the integration of CAM with CAD systems solidified the CAM philosophy. This synergy sped up production times and enhanced product quality. Industries began to recognize the benefits of a more holistic approach to manufacturing—designers and engineers working together, utilizing software to manipulate and optimize components.
As a result, by the 2000s, CAM systems became widely adopted across various sectors including automotive and aerospace manufacturing. This integration fostered advancements in automation, leading to the adoption of robotics and the Internet of Things (IoT) technologies in production environments. Today, CAM represents an essential part of advanced manufacturing processes, impacting everything from small workshops to large industrial facilities.
Understanding the historical development of CAM is fundamental for IT professionals, software engineers, and business leaders alike. It sheds light on the technological achievements that have made modern methods possible, highlighting the perpetual interconnection between design, machinery, and software in contemporary manufacturing.
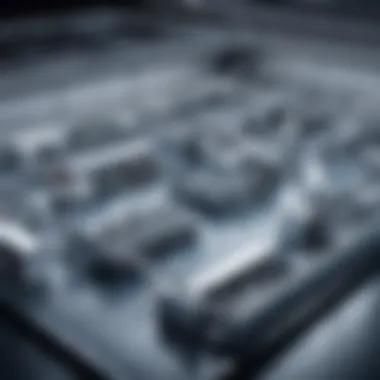
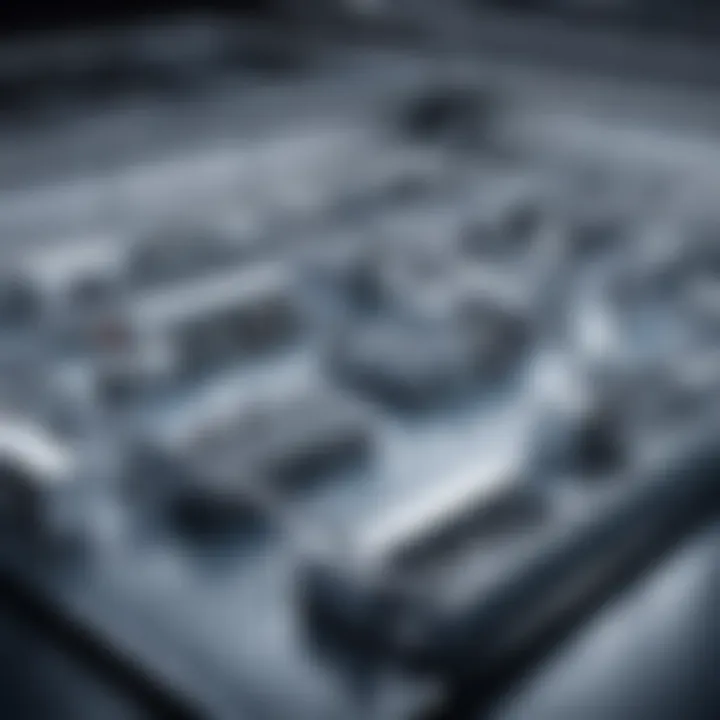
Core Components of CAM
In the landscape of Computer Aided Manufacturing, understanding the core components is essential. These elements establish the foundation of how CAM systems operate. Their integration profoundly affects productivity, efficiency, and the overall quality of the finished product. Recognizing these components enables companies to make informed decisions, enhancing their manufacturing processes.
Software Solutions
Software solutions form the backbone of CAM systems. They facilitate complex processes from design to production. These programs allow users to create detailed, precise models that the machinery can interpret. A few widely-used software applications in the market include Autodesk Fusion 360, SolidWorks, and Mastercam.
The choice of software can influence the capabilities of a CAM setup. Some applications focus on specific industries, like Siemens NX for aerospace, while others offer more broad functionality. Not only do these tools enable detailed modeling, but they also optimize tool paths, which directly impacts machining speed and material usage. Furthermore, software updates are frequent, offering new features and improvements, which keeps systems competitive.
Additionally, many software solutions support integration with Computer Aided Design (CAD) systems. This compatibility ensures a seamless workflow from design to manufacturing. Therefore, choosing the right software solution is not just about features; it is about long-term adaptability to industry changes.
Hardware Requirements
While software is crucial, hardware components also play a significant role in the effectiveness of CAM systems. The correct hardware ensures machines operate at their optimal levels. Key hardware aspects include CNC machines, workstations, and input devices.
CNC machines are at the heart of manufacturing in CAM. These machines translate digital plans into physical products through high precision. They come in various types, such as milling machines and lathes, each suitable for different applications. The choice of machine often depends on the material being used and the desired outcome.
Moreover, robust workstations are necessary to handle the software's computational demands. High-performance processors, ample RAM, and dedicated graphics cards are essential features for handling complex calculations and rendering models efficiently.
In summary, the core components of CAM—software and hardware—work together to create an efficient manufacturing environment. Understanding these elements allows businesses to select the right tools and systems that align with their operational goals. The significance of this knowledge cannot be overstated, as improved systems lead to increased output and reduced production times.
Integration with Computer Aided Design (CAD)
The integration of Computer Aided Manufacturing (CAM) with Computer Aided Design (CAD) has fundamentally transformed the manufacturing landscape. This synergy enhances design quality and precision and facilitates a seamless transition from concept to production. Understanding the importance of CAD-CAM linkage is critical for professionals looking to leverage technology in their processes.
Importance of CAD-CAM Linkage
The CAD-CAM connection plays a crucial role in modern manufacturing processes. It serves as a bridge between design and manufacturing, enabling a more collaborative environment. With advanced software, designers can create intricate models that engineers can study to produce efficient machining operations. This reduces the risk of errors during production, as changes made in the design can immediately reflect in the manufacturing process.
Furthermore, this linkage allows for rapid prototyping. Designers create a digital model, and CAM systems can use this directly to produce prototypes. This leads to faster product development cycles, providing manufacturers with a competitive edge. By simplifying communication between design teams and production units, a CAD-CAM integrated system enhances overall productivity.
Streamlined Workflow
A streamlined workflow is essential for maximizing efficiency in manufacturing. The integration of CAD and CAM creates a continuous flow of information. Design files created in CAD software are directly available to CAM systems, which drastically reduces the time spent on data transfer and formatting.
Specific benefits include:
- Reduced Lead Times: Faster information transfer ensures quicker turnaround from design to manufacturing.
- Minimized Errors: Automated sharing of design specifications reduces the chances of miscommunication, preventing costly errors.
- Increased Flexibility: Design modifications can be implemented swiftly in the manufacturing process, adapting easily to changing market demands.
Applications of CAM
Understanding the applications of Computer Aided Manufacturing (CAM) is crucial for grasping its significance in the modern manufacturing landscape. CAM plays an essential role in streamlining production processes, enhancing product quality, and reducing time to market. Different sectors leverage CAM technology, each with distinct needs and advantages.
Automotive Industry
In the automotive sector, CAM systems are integral to improving efficiency in vehicle production. Manufacturers utilize CAM for tasks such as precision machining of components, assembly line automation, and quality control measures.
By implementing CAM, automotive companies benefit from:
- Enhanced accuracy: CAM reduces human error in manufacturing, leading to tight tolerances in critical components like engine parts.
- Rapid prototyping: The ability to quickly develop prototypes helps manufacturers test designs efficiently before full-scale production.
- Inventory management: CAM allows for just-in-time production, minimizing excess inventory and reducing storage costs.
These efficiencies translate into lower costs and improved profitability for automotive manufacturers.
Aerospace Manufacturing
The aerospace industry demands high standards for precision and safety. CAM provides tools that meet these stringent requirements. Aerospace components often have complex geometries and tight specifications.
Key benefits in this sector include:
- Complex part production: CAM enables the production of intricate components like turbine blades and fuselage structures.
- Continuous monitoring: Real-time data from CAM systems facilitates ongoing quality checks throughout the manufacturing process.
- Regulatory compliance: CAM supports adherence to various regulatory standards essential in aerospace, ensuring that components are built to required specifications.
Thus, CAM is vital for the aerospace industry's focus on safety and innovation.
Consumer Products
In the consumer goods sector, CAM applications vary widely, from electronics to home goods. The flexibility of CAM systems allows manufacturers to adapt quickly to changing market demands.
Advantages for consumer product manufacturing include:
- Customization: CAM supports personalized production, enabling companies to cater to individual consumer preferences.
- Cost-effectiveness: By optimizing production schedules and minimizing waste, CAM can enhance profitability for businesses producing consumer products.
- Faster production cycles: Improved workflows lead to quicker turnaround times, assisting companies in getting items to market promptly.
The ability to respond to consumer trends swiftly is essential in this competitive industry.
The applications of CAM are diverse and impactful, influencing efficiency and quality across various manufacturing sectors. As businesses embrace these technologies, they position themselves for sustained competitive advantages.
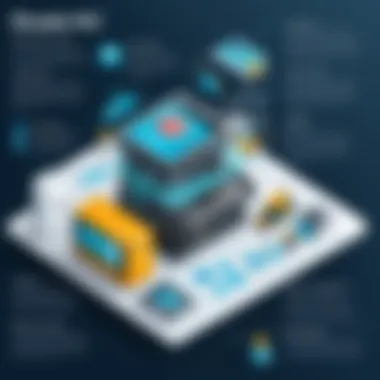
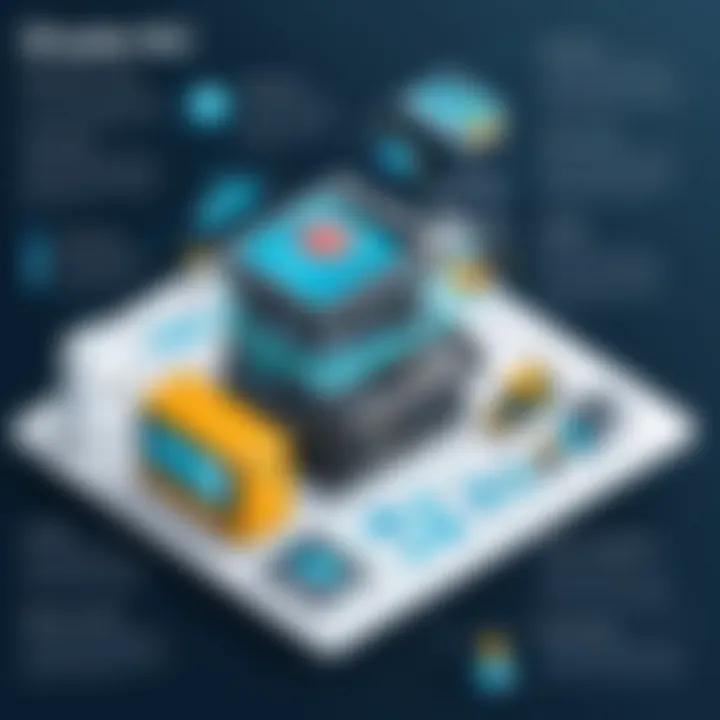
Benefits of CAM
Computer Aided Manufacturing (CAM) holds significant importance in the realm of modern manufacturing. The advantages it provides are not just instrumental for efficiency but also critical for maintaining a competitive edge in various industries. As manufacturers strive to meet the demands of quality, speed, and adaptability, CAM emerges as a cornerstone of contemporary production strategies. Insight into its benefits offers businesses a clearer understanding of why adopting CAM technologies is essential.
Enhanced Precision
Precision is paramount in manufacturing. CAM systems greatly enhance production accuracy by applying computer-based controls and automated processes. This increase in precision results from the ability to minimize human error and maintain consistency across different production runs. The software used in CAM allows for precise modeling of parts and components.
Moreover, CAM systems often employ high-quality tools and equipment, ensuring that the outputs match their design specifications closely. This not only reduces waste material but also aligns with quality standards required in sectors such as aerospace and medical devices. In practical terms, a manufacturer utilizing CAM may experience fewer product recalls due to errors, bolstering their reputation.
Increased Efficiency
Efficiency is a key motivator behind the integration of CAM. By automating the production process, CAM reduces the time needed to create complex components. Processes that would typically take hours can be completed in minutes. This time-saving aspect allows manufacturers to increase their output without compromising quality.
Increased efficiency also correlates with the optimal use of resources. CAM systems can calculate the best strategies for using raw materials. In turn, this can lead to significant reductions in cycle times, enabling quicker turnaround on projects. With workflows streamlined, teams can focus on value-added activities rather than getting caught up in manual tasks.
Cost Reduction
Implementing CAM often leads to notable cost reductions. While the initial investment in software and equipment might be significant, the long-term savings tend to outweigh these expenses. Reduced errors and waste translate to lower material costs. The efficiencies gained can also mean fewer labor costs, as tasks that required multiple personnel can often be handled by a single operator overseeing the automated system.
In addition, companies that adopt CAM can respond faster to changes in orders or demand fluctuations, allowing them to allocate resources more effectively and maintain profitability.
"An investment in CAM leads to benefits that escalate over time, from improved production precision to significant reductions in operational costs."
In summary, the benefits of CAM—enhanced precision, increased efficiency, and reduced costs—make it an invaluable asset for manufacturers. Understanding these advantages is critical for IT professionals and businesses seeking to improve their production capabilities and adapt to an ever-evolving market.
Challenges in Implementing CAM
While the potential benefits of Computer Aided Manufacturing (CAM) are considerable, various challenges hinder successful implementation. These challenges demand awareness from professionals and businesses considering CAM adoption. Addressing these issues is crucial for seamless integration and smooth operations in manufacturing environments.
High Initial Investment
One of the most significant challenges in CAM implementation is the high initial investment required. Introducing CAM technology necessitates substantial financial commitment. This can encompass expenses like purchasing software licenses, acquiring specialized hardware, and training personnel. In many cases, the cost of upgrading existing systems can also be considerable. For small to medium-sized enterprises, these costs can be especially daunting.
Many organizations perform a cost-benefit analysis before deciding to invest in CAM systems. However, the return on investment may only become evident after a considerable duration. Companies must weigh the long-term efficiencies that CAM can provide against the upfront expenditure. The initial hurdles may be intimidating, but understanding potential gains related to productivity and accuracy can guide decision-making.
Skill Shortages
Another challenge in implementing CAM systems is the shortage of skilled personnel. The integration of sophisticated CAM technology requires users to possess specialized training and experience. However, there exists a gap in the workforce equipped with the necessary skills. Many educational institutions have not sufficiently adapted their curricula to meet the demands of modern manufacturing, creating an imbalance in available talent.
Organizations may find themselves investing not only in technology but also in training programs. This dual investment can stretch resources. Furthermore, attracting talent skilled in CAM and related technologies can be difficult in competitive industries. Organizations may need to implement strategies to develop their workforce, ensuring they have the expertise to operate and maintain CAM systems effectively.
Integration Issues
Lastly, integration issues present a notable challenge when adopting CAM. This primarily involves coordinating new CAM systems with existing workflows and technologies. If CAM does not seamlessly integrate with Computer Aided Design (CAD) platforms, it can lead to significant disruptions in production processes.
Furthermore, organizations must ensure that all departments are aligned, from design to production. A lack of compatibility between software and hardware can create bottlenecks. Such challenges may require additional IT support to ensure successful integration. Planning and executing a comprehensive integration strategy can mitigate these risks, but it requires careful attention to detail and thorough testing.
"Successful implementation of CAM is not just about technology; it's also about people and processes."
In summary, while CAM presents numerous advantages, it is not without challenges. High initial investments, skill shortages, and integration issues require strategic planning. Manufacturers need to approach these hurdles with a focus on long-term benefits, ensuring they can leverage CAM technology effectively.
Future Trends in Computer Aided Manufacturing
The landscape of Computer Aided Manufacturing (CAM) is evolving rapidly. Staying updated on future trends is crucial for companies aiming not only to survive but thrive in a competitive marketplace. Embracing new technologies can enhance efficiency, reduce costs, and improve production quality. In this section, we examine three significant trends: automation and robotics, artificial intelligence, and sustainable manufacturing practices.
Automation and Robotics
Automation is a critical driver in the transformation of manufacturing processes. It involves the use of machines and technology to perform tasks with minimal human intervention. Robotics, in particular, is reshaping how factories operate. Robots improve precision in tasks like welding, painting, and assembly. They work tirelessly, reducing errors caused by tiredness or human fatigue.
Benefits of Automation and Robotics:
- Increased efficiency: Automating repetitive tasks allows employees to focus on more complex issues.
- Enhanced quality control: Robots execute tasks consistently, leading to uniformity in products.
- Safety improvements: Dangerous jobs can be handed over to machines, thereby keeping human workers safe.
The integration of robotics into CAM systems enables manufacturers to create more agile and responsive production lines. As technology advances, we expect to see a decrease in costs associated with robotics, making it accessible to smaller enterprises.
Artificial Intelligence in CAM
Artificial intelligence (AI) is making inroads into CAM by predicting outcomes and optimizing processes. AI algorithms can analyze vast amounts of data from manufacturing operations. This enables real-time adjustments to be made, improving both quality and efficiency.
Key impacts of AI on CAM include:
- Predictive maintenance: Machines equipped with AI can alert operators of potential breakdowns before they occur, minimizing downtime.
- Enhanced decision-making: AI provides insights from historical data, allowing manufacturers to make informed choices swiftly.
- Customization: AI enables manufacturers to adjust production processes for tailored solutions, helping to meet specific customer demands.
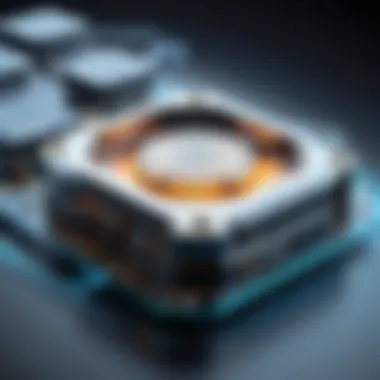
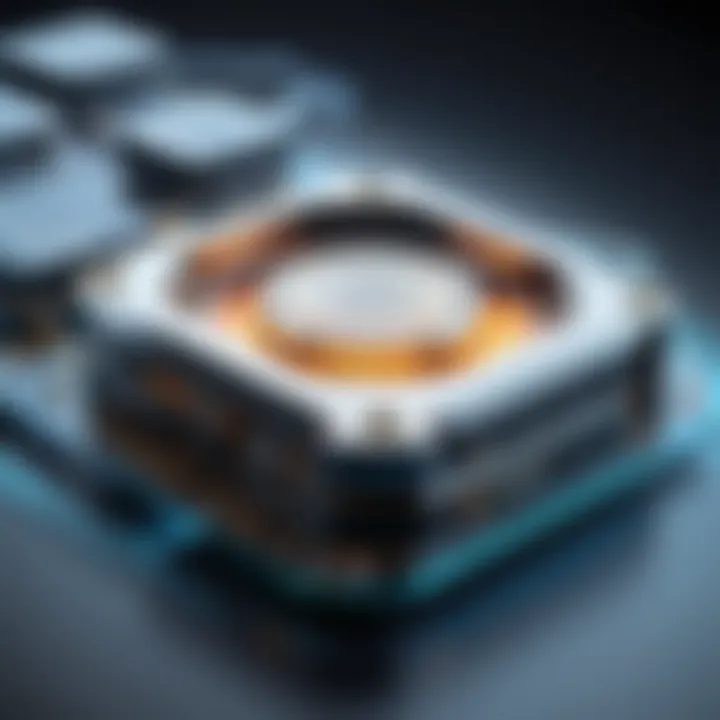
The marriage of AI and CAM creates opportunities for innovation. Companies that harness this technology stand to gain a competitive edge in their respective markets.
Sustainable Manufacturing Practices
As global awareness of environmental issues grows, so does the need for sustainable practices in manufacturing. CAM can contribute significantly to this cause by optimizing resource use and minimizing waste.
Sustainable practices include:
- Energy-efficient processes: CAM systems can optimize energy use, resulting in reduced costs and carbon footprints.
- Material reduction: Advanced CAM techniques can minimize scrap production and more effectively utilize raw materials.
- Lifecycle assessments: These assessments monitor the environmental impact of a product throughout its life, encouraging manufacturers to adopt greener alternatives.
Sustainability not only meets regulatory requirements but also appeals to a growing demographic of environmentally conscious consumers. Companies integrating sustainable practices into their CAM systems will likely see consumer loyalty and positive brand perception.
The future of CAM is not just about technology; it’s about creating systems that are efficient, intelligent, and sustainable.
Case Studies: Successful CAM Implementations
Examining successful implementations of Computer Aided Manufacturing (CAM) allows us to understand its full potential and advantages in real-world scenarios. Case studies provide concrete examples that illustrate the operational efficiencies and innovation that can arise from effectively integrating CAM into manufacturing processes. They also offer insights into challenges faced and solutions found, enriching our understanding of the practical applications of CAM across various industries. Moreover, these examples highlight the strategic importance of adopting CAM technologies, not only for boosting productivity but also for maintaining competitive advantage in a rapidly evolving market.
Case Study One: Automotive Sector
The automotive sector has been at the forefront of adopting Computer Aided Manufacturing. Companies like Ford Motor Company showcase how CAM enhances production lines. Ford integrated advanced CAM solutions to improve the precision and speed of manufacturing. The use of automated milling machines and robots significantly streamlined the production process.
Key benefits observed in Ford's implementation include:
- Increased Precision: The CNC machines enabled tighter tolerances, ensuring components fit accurately during assembly.
- Efficiency Boost: Automated processes led to faster production cycles and reduced downtime.
- Quality Control: CAM systems monitor production in real-time, leading to fewer defects.
This case study illustrates that with the right CAM tools, automotive manufacturers can respond quickly to market demands while maintaining high standards of quality.
Case Study Two: Aerospace Industry
In the aerospace industry, Boeing serves as a prime example of successful CAM utilization. The implementation of CAM at Boeing has drastically improved its manufacturing capabilities, especially in the assembling of complex aircraft components. Boeing adopted sophisticated CAM software to facilitate designs from CAD, which streamlined workflow and reduced errors during production.
Key evidence of success in Boeing's approach includes:
- Reduced Lead Times: CAM allows for faster prototyping and manufacturing, which is crucial in aerospace where innovation is constant.
- Cost Effectiveness: By minimizing material waste and optimizing production processes, Boeing has significantly reduced production costs.
- Enhanced Customization: CAM systems enable better adaptations for custom orders, catering to specific client requirements.
Ultimately, these studies affirm that integrating CAM into manufacturing can yield transformative results, aiding in precision, speed, and cost management. Through continual improvement and innovation, companies in the automotive and aerospace sectors illustrate why CAM remains critical in modern manufacturing.
Regulatory and Compliance Issues
Regulatory and compliance issues hold a critical position in Computer Aided Manufacturing (CAM). They ensure that the production process adheres to industry standards, legal requirements, and safety regulations. In the landscape of modern manufacturing, following these regulations is essential for avoiding legal ramifications and establishing a reputable brand.
Standards in Manufacturing
Standards in manufacturing relate to guidelines that define acceptable practices and performance criteria. They serve several key purposes:
- Safety Assurance: Standards help protect workers by enforcing safety measures in operating equipment. This creates a safer workplace environment.
- Quality Control: Adhering to standards means consistent quality in products. This reduces the likelihood of defects and increases customer satisfaction.
- Interoperability: Manufacturing entities often rely on equipment from various suppliers. Standards ensure compatibility between different machines and software, facilitating seamless integration.
- Market Access: Many markets require compliance with specific standards to enter. For businesses looking to expand internationally, understanding and meeting these regulations is crucial for success.
Notable organizations such as ISO (International Organization for Standardization) and ANSI (American National Standards Institute) provide frameworks for these standards, guiding manufacturers on best practices.
Safety Compliance
Safety compliance in CAM encompasses regulations designed to minimize hazards associated with machinery and manufacturing processes. Understanding these regulations is vital for several reasons:
- Risk Mitigation: By adhering to safety compliance, businesses can significantly reduce workplace accidents and injuries. This not only protects employees but also lowers insurance costs.
- Legal Requirements: Many countries enforce laws concerning workplace safety. Non-compliance can lead to heavy fines and legal consequences.
- Employee Morale: A commitment to safety contributes to a positive workplace culture. Employees feel valued when their safety is prioritized, leading to increased productivity.
- Regulatory Audits: Regular compliance audits help identify potential safety gaps. They also reinforce a commitment to adhering to industry standards.
Key Considerations
"Regulatory compliance is not just about avoiding fines; it’s about fostering an organization that values quality, safety, and operational excellence."
In light of these regulations, businesses engaged in CAM must:
- Stay updated on ever-changing regulations.
- Train employees thoroughly on safety procedures and compliance requirements.
- Implement robust reporting and documentation systems.
Investing time and resources into regulatory and compliance issues yields significant long-term benefits. It enhances an organization's reputation and ensures a sustainable manufacturing operation.
Epilogue: The Future of CAM
As the landscape of manufacturing continues to evolve, the future of Computer Aided Manufacturing (CAM) emerges as a critical topic that deserves attention. Understanding the direction in which CAM is heading is essential not only for IT professionals and software developers but also for business owners who rely on efficient production systems. The integration of advanced technologies like automation, artificial intelligence, and sustainable practices into CAM systems will dictate how companies operate in coming years.
One significant element of this future is the increasing reliance on automation and robotics. With machines taking over repetitive tasks, human operators can focus on more critical aspects of the production process. This not only enhances productivity but also reduces the potential for human error. Furthermore, the synergy between CAM and robotics allows for the creation of intricate designs that would be impossible to achieve with traditional manufacturing methods.
Incorporating artificial intelligence into CAM will also play a pivotal role. AI-driven systems can analyze large datasets to optimize workflows, forecast maintenance needs, and improve production efficiency. This predictive capability can greatly reduce downtime and operational costs.
Sustainable manufacturing practices will form another cornerstone of CAM's future. As industries face growing pressure to reduce waste and energy consumption, CAM technology will adapt to include eco-friendly processes. This shift will not only be driven by regulation but also by consumer demand for greener products. Manufacturers that harness sustainability-driven CAM technologies will likely gain a competitive advantage.
It is essential to consider that while these trends present numerous benefits, they also come with challenges. High initial investments in new technologies and a potential skills gap in the workforce could hinder progress. Businesses must prioritize training and education to prepare their teams for the future.
Thus, staying informed about advancements in CAM is critical for business strategy and operational success in a rapidly changing environment.
In summary, the future of CAM holds transformative potential. By understanding these trends and their implications, IT professionals, software experts, and business leaders can position their organizations for success in a competitive landscape. Engaging with CAM technologies is not merely an option; it is a necessity for those seeking to lead in their industries.